Micropore type coating sizing and preparation method thereof
A coating slurry and microporous technology, applied in textiles, papermaking, fiber processing, etc., can solve the problems of internal solvent volatilization, influence on use, system instability, etc., and achieve the effect of compensating for volatilization, convenient processing, and good competitive advantage.
- Summary
- Abstract
- Description
- Claims
- Application Information
AI Technical Summary
Problems solved by technology
Method used
Examples
Embodiment 1
[0017] Weigh each raw material according to parts by weight: 100 parts of aromatic polyether polyurethane, 20 parts of toluene, 20 parts of methyl ethyl ketone, 4 parts of multifunctional aliphatic isocyanate, 4 parts of fatty ester, 3 parts of fluorocarbon resin, 45 parts of water Add polyurethane resin, toluene and methyl ethyl ketone into the mixer respectively, and stir at high speed for 3 minutes; add multifunctional aliphatic isocyanate, fatty ester compound and fluorocarbon resin into the mixer in turn, and stir at high speed for 4 minutes after each additive is added , form an oily slurry; add water into the mixer after atomization, and stir at a high speed for 3 minutes to form a white emulsion slurry; pour the above slurry into a container, spray 0.5 parts of methyl ethyl ketone solvent on its surface, and then put The container is sealed to obtain a finished product.
Embodiment 2
[0019] Weigh each raw material in parts by weight: 100 parts of aromatic polyether polyurethane, 15 parts of toluene, 15 parts of butanone, 2 parts of aromatic polyisocyanate, 1 part of fatty ester, 1 part of silicone resin, 60 parts of water Add polyurethane resin, toluene and butanone into the mixer respectively, and stir at high speed for 2 minutes; add multifunctional aliphatic isocyanate, fatty ester and fluorocarbon resin into the mixer in sequence, and stir at high speed for 3 minutes after each additive is added. Form an oily slurry; add water into the mixer after atomization, and stir at high speed for 4 minutes to form a white emulsion slurry; pour the above slurry into a container, spray 0.5 parts of butanone solvent on the surface, and then put the container Seal it to get the finished product.
Embodiment 3
[0021] Weigh each raw material in parts by weight: 100 parts of aromatic polyether polyurethane, 25 parts of toluene, 25 parts of butanone, 6 parts of aromatic polyisocyanate, 5 parts of fatty ester, 5 parts of fluorocarbon resin, and 30 parts of water Add polyurethane resin, toluene and methyl ethyl ketone into the mixer respectively, and stir at high speed for 2 minutes; add multifunctional aliphatic isocyanate, fatty esterified product and fluorocarbon resin into the mixer in sequence, and stir at high speed for 5 minutes after each additive is added. Form an oily slurry; add water into the mixer after atomization, and stir at high speed for 2 minutes to form a white emulsion slurry; pour the above slurry into a container, spray 0.5 parts of methyl ethyl ketone solvent on the surface, and then put the container Seal it to get the finished product.
PUM
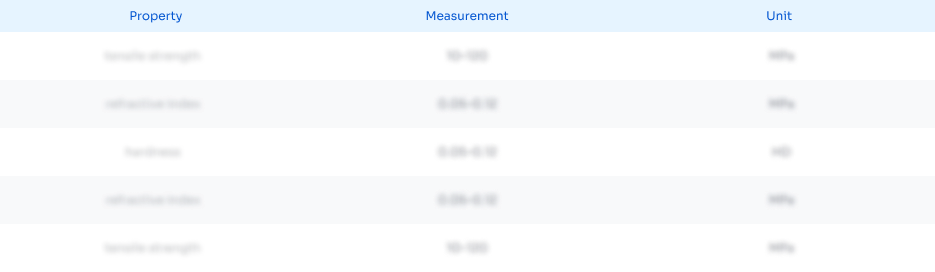
Abstract
Description
Claims
Application Information

- Generate Ideas
- Intellectual Property
- Life Sciences
- Materials
- Tech Scout
- Unparalleled Data Quality
- Higher Quality Content
- 60% Fewer Hallucinations
Browse by: Latest US Patents, China's latest patents, Technical Efficacy Thesaurus, Application Domain, Technology Topic, Popular Technical Reports.
© 2025 PatSnap. All rights reserved.Legal|Privacy policy|Modern Slavery Act Transparency Statement|Sitemap|About US| Contact US: help@patsnap.com