Superfine fiber leather and preparation method thereof
A technology of superfine fiber leather and additives, which is applied in the direction of chemical instruments and methods, textiles and papermaking, synthetic resin layered products, etc. It can solve the problems of poor moisture permeability and difficulty in simultaneously improving moisture permeability and wear resistance. Achieve the effect of improving wearing life and improving comfort
- Summary
- Abstract
- Description
- Claims
- Application Information
AI Technical Summary
Problems solved by technology
Method used
Image
Examples
Embodiment 1
[0044] The formula of dry slurry is:
[0045] Surface layer: 60 parts of polyurethane resin (TQS-1), 40 parts of polyurethane resin (TQS-5), 30 parts of DMF, 30 parts of MEK, 5 parts of colorant, 3 parts of anti-friction additive 9206-F, hydrophilic additive DS -32991.5 copies.
[0046] Middle layer: 50 parts of polyurethane resin (TQS-1), 50 parts of polyurethane resin (TQS-5), 20 parts of DMF, 30 parts of MEK, 5 parts of colorant, 3 parts of anti-friction additive 9206-F, hydrophilic additive DS- 32991.5 copies.
[0047] Adhesive layer: 100 parts of polyurethane resin (JF-A-5025), 80 parts of water-absorbing resin (Yilicheng 2009X), 10 parts of MEK, 1 part of anti-friction additive 9206-F, 1 part of hydrophilic additive DS-3299.
[0048] Microfiber leather preparation method:
[0049] (1) Preparation of dyed base fabric: Nylon 6 (PA6) and low-density polyethylene (LDPE) are blended and spun to make a non-woven fabric. After ironing, impregnate polyurethane resin (PU), and...
Embodiment 2
[0052] The formula of dry slurry is:
[0053] Surface layer: 60 parts of polyurethane resin (TQS-1), 40 parts of polyurethane resin (TQS-5), 30 parts of DMF, 30 parts of MEK, 5 parts of colorant, 6 parts of anti-friction additive 9206-F, hydrophilic additive DS -32991.5 copies.
[0054] Middle layer: 50 parts of polyurethane resin (TQS-1), 50 parts of polyurethane resin (TQS-5), 20 parts of DMF, 30 parts of MEK, 5 parts of colorant, 6 parts of anti-friction additive 9206-F, hydrophilic additive DS- 32991.5 copies.
[0055] Adhesive layer: 100 parts of polyurethane resin (JF-A-5025), 80 parts of water-absorbing resin (Yilicheng 2009X), 10 parts of MEK, 6 parts of anti-friction additive 9206-F, 1 part of hydrophilic additive DS-3299.
[0056] Microfiber leather preparation method:
[0057] (1) with embodiment 1 step (1);
[0058] (2) Dry veneer: apply a layer of layer slurry on the release paper, dry it in an oven, then apply a layer of middle layer slurry, dry it in an oven...
Embodiment 3
[0060] The formula of dry slurry is:
[0061] Surface layer: 60 parts of polyurethane resin (TQS-1), 40 parts of polyurethane resin (TQS-5), 30 parts of DMF, 30 parts of MEK, 5 parts of colorant, 3 parts of anti-friction additive 9206-F, hydrophilic additive DS -32995 copies.
[0062] Middle layer: 50 parts of polyurethane resin (TQS-1), 50 parts of polyurethane resin (TQS-5), 20 parts of DMF, 30 parts of MEK, 5 parts of colorant, 3 parts of anti-friction additive 9206-F, hydrophilic additive DS- 32995 copies.
[0063] Adhesive layer: 100 parts of polyurethane resin (JF-A-5025), 80 parts of water-absorbing resin (Yilicheng 2009X), 10 parts of MEK, 1 part of anti-friction additive 9206-F, 5 parts of hydrophilic additive DS-32999.
[0064] Microfiber leather preparation method:
[0065] (1) with embodiment 1 step (1);
[0066] (2) Dry veneer: apply a layer of layer slurry on the release paper, dry it in an oven, then apply a layer of middle layer slurry, dry it in an oven, a...
PUM
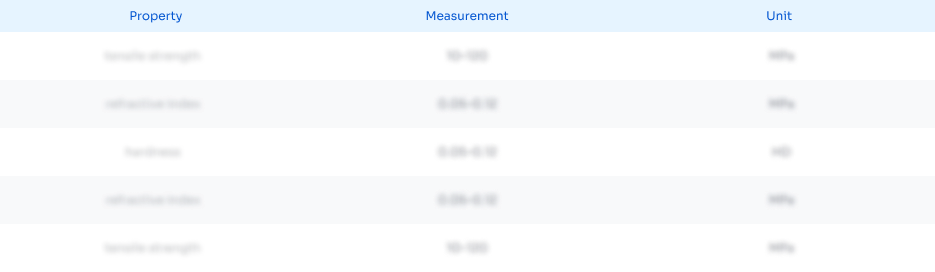
Abstract
Description
Claims
Application Information

- Generate Ideas
- Intellectual Property
- Life Sciences
- Materials
- Tech Scout
- Unparalleled Data Quality
- Higher Quality Content
- 60% Fewer Hallucinations
Browse by: Latest US Patents, China's latest patents, Technical Efficacy Thesaurus, Application Domain, Technology Topic, Popular Technical Reports.
© 2025 PatSnap. All rights reserved.Legal|Privacy policy|Modern Slavery Act Transparency Statement|Sitemap|About US| Contact US: help@patsnap.com