Manufacturing method for copper interconnection lines
A manufacturing method and interconnection wire technology, which are applied in semiconductor/solid-state device manufacturing, electrical components, circuits, etc., to achieve the effect of reducing etching steps, reducing manufacturing costs, and increasing productivity
- Summary
- Abstract
- Description
- Claims
- Application Information
AI Technical Summary
Problems solved by technology
Method used
Image
Examples
Embodiment Construction
[0031] The specific embodiment of the present invention will be further described below in conjunction with accompanying drawing:
[0032] Figures 3a-3i It is a schematic structural flow diagram of a copper interconnection method of the present invention;
[0033] Such as Figures 3a-3i As shown in the present invention, a method for manufacturing a copper interconnection line of the present invention, first, deposit a low dielectric constant dielectric layer 32 on the upper surface of a silicon substrate 31, and coat the first photoresist 33 that can form a hard mask to cover the dielectric layer 32, after exposure and development, the excess photoresist is removed to form a first hard mask photoresist 331 with a metal groove structure 34; wherein, the material of the first photoresist 33 contains silane groups, silane oxides Base or clathrate siloxane, etc.
[0034] Next, in the same developing station, coat the miniaturized cured material 35 such as miniaturized cured f...
PUM
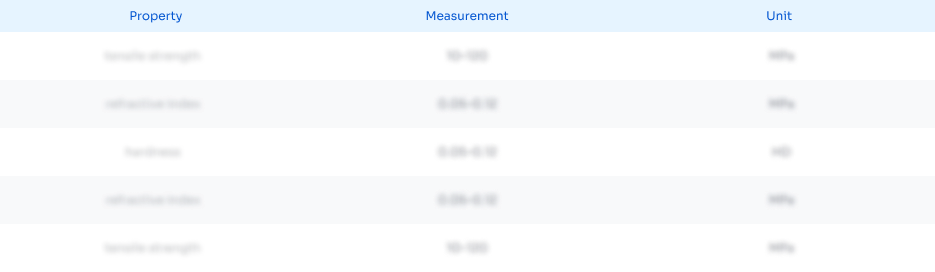
Abstract
Description
Claims
Application Information

- R&D
- Intellectual Property
- Life Sciences
- Materials
- Tech Scout
- Unparalleled Data Quality
- Higher Quality Content
- 60% Fewer Hallucinations
Browse by: Latest US Patents, China's latest patents, Technical Efficacy Thesaurus, Application Domain, Technology Topic, Popular Technical Reports.
© 2025 PatSnap. All rights reserved.Legal|Privacy policy|Modern Slavery Act Transparency Statement|Sitemap|About US| Contact US: help@patsnap.com