Method for preparing terephthalic acid ester plasticizer with pressurization method
A technology for terephthalate and terephthalic acid, applied in the field of synthesizing terephthalate plasticizers, can solve the problems of unsuitability for industrial production, long process cycle, long reaction time, etc., and achieve product separation Simple and efficient purification, promotion of diffusion, and stable product performance
- Summary
- Abstract
- Description
- Claims
- Application Information
AI Technical Summary
Problems solved by technology
Method used
Image
Examples
Embodiment 1
[0037] In the first step, according to the mass ratio, mix 100 parts of purified terephthalic acid, 160 parts of isooctyl alcohol, and 0.5 parts of tetrabutyl titanate into the high-pressure reactor, set the pressure threshold to 0.10 MPa, raise the temperature and pressurize, when When the temperature rises to 180 °C, start stirring, control the stirring speed at 1000 r / min, maintain the reaction temperature at 180 °C, and react for 3 h under the threshold pressure, and the acid value of the product is ≤1. During the reaction process, when the reaction pressure exceeds the set threshold, the pressure reducing valve will automatically open, exhaust and adjust the pressure, and the exhausted gas will be recovered after being condensed.
[0038] In the second step, after the reaction is completed, cooling water is passed through the kettle body. When the temperature is lower than 180 ° C, the gas outlet valve is opened to discharge the remaining gas, which is recovered after cond...
Embodiment 2
[0042] In the first step, according to the mass ratio, mix 100 parts of purified terephthalic acid, 240 parts of isooctyl alcohol, and 2.5 parts of tetrabutyl titanate into the high-pressure reactor, set the pressure threshold to 1.6 MPa, raise the temperature and pressurize, when When the temperature rises to 180°C, start the stirring, control the stirring speed at 1000 r / min, continue to raise the temperature to 250°C, and react at the threshold pressure for 1 hour, and the acid value of the product is ≤1. During the reaction process, when the reaction pressure exceeds the set threshold, the pressure reducing valve will automatically open, exhaust and adjust the pressure, and the exhausted gas will be recovered after being condensed.
[0043] In the second step, after the reaction is completed, the cooling water is passed through the kettle body. When the temperature is lower than 180°C, the gas outlet valve is opened to discharge the remaining gas, which is recovered after c...
Embodiment 3
[0047] In the first step, according to the mass ratio, mix 100 parts of purified terephthalic acid, 240 parts of isooctyl alcohol, and 2.5 parts of tetraisobutyl titanate into the high-pressure reactor, set the pressure threshold to 1.0 MPa, raise the temperature and pressurize, When the temperature rises to 180°C, start stirring, control the stirring speed at 1000 r / min, continue to raise the temperature to 220°C, and react for 2 hours under the threshold pressure, and the acid value of the product is ≤1. During the reaction process, when the reaction pressure exceeds the set threshold, the pressure reducing valve will automatically open, exhaust and adjust the pressure, and the exhausted gas will be recovered after being condensed.
[0048] In the second step, after the reaction is completed, the cooling water is passed through the kettle body. When the temperature is lower than 180°C, the gas outlet valve is opened to discharge the remaining gas, which is recovered after con...
PUM
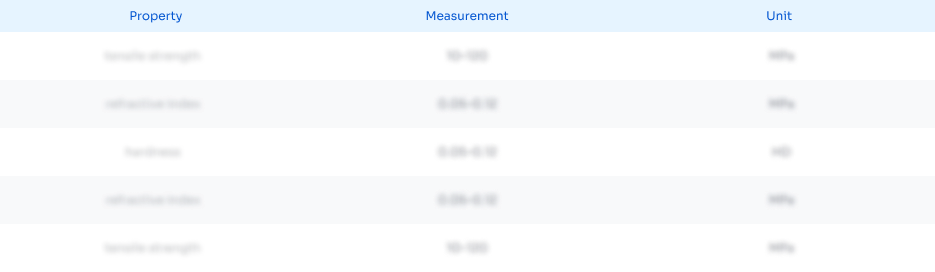
Abstract
Description
Claims
Application Information

- Generate Ideas
- Intellectual Property
- Life Sciences
- Materials
- Tech Scout
- Unparalleled Data Quality
- Higher Quality Content
- 60% Fewer Hallucinations
Browse by: Latest US Patents, China's latest patents, Technical Efficacy Thesaurus, Application Domain, Technology Topic, Popular Technical Reports.
© 2025 PatSnap. All rights reserved.Legal|Privacy policy|Modern Slavery Act Transparency Statement|Sitemap|About US| Contact US: help@patsnap.com