Water-based polyurethane enamel paint
A water-based polyurethane and enamel technology, used in polyurea/polyurethane coatings, coatings, etc., can solve problems such as damage to the health of construction workers, fire hazards, and environmental pollution.
- Summary
- Abstract
- Description
- Claims
- Application Information
AI Technical Summary
Problems solved by technology
Method used
Examples
example 1
[0024] A water-based polyurethane enamel is formed by mixing component A and component B according to a 7:1 weight ratio, wherein the component A is composed as follows by weight ratio:
[0025] 100 parts of water-based acrylic grafted polyurethane emulsion, 26 parts of titanium dioxide, 0.5 parts of bismuth vanadate yellow,
[0026] 20 parts of functional filler, 0.5 parts of rheological agent,
[0027] Wetting and dispersing agent 0.5 parts, substrate wetting agent 0.5 parts,
[0028] 0.5 parts of anti-settling agent, 0.5 parts of defoamer,
[0029] 0.5 part of thickener, 0.5 part of leveling agent;
[0030] Described component B is composed as follows by weight and number ratio:
[0031] 15 parts of isocyanates, 15 parts of dipropylene glycol dimethyl ether ;
[0032] Among them, the functional filler is composed of fumed silica, decabromodiphenyl ether, antimony trioxide and zinc borate, which are mixed in 1.2 parts, 10.5 parts, 1.75 parts and 1.75 parts respectivel...
Embodiment 2
[0034] A water-based polyurethane enamel is formed by mixing component A and component B according to a 7:1 weight ratio, wherein the component A is composed as follows by weight ratio:
[0035] 100 parts of water-based acrylic grafted polyurethane emulsion, 5 parts of titanium dioxide, 20 parts of red face powder,
[0036] 10 parts of functional filler, 0.2 parts of rheological agent,
[0037] Wetting and dispersing agent 0.1 part, substrate wetting agent 0.1 part,
[0038] 0.2 parts of anti-settling agent, 0.2 parts of defoaming agent,
[0039] 0.2 part of thickener, 0.1 part of leveling agent;
[0040] Described component B is composed as follows by weight and number ratio:
[0041] 10 parts of isocyanates, 10 parts of dipropylene glycol dimethyl ether ;
[0042] The functional filler components described in it are the same as those in Example 1.
Embodiment 3
[0044] A water-based polyurethane enamel is formed by mixing component A and component B according to a 7:1 weight ratio, wherein the component A is composed as follows by weight ratio:
[0045] 100 parts of water-based acrylic grafted polyurethane emulsion, 10 parts of titanium dioxide,
[0046] 5 parts of red face powder, 4 parts of phthalocyanine blue, 6 parts of bismuth vanadate yellow,
[0047] 15 parts of functional filler, 0.35 parts of rheological agent,
[0048] 0.3 parts of wetting and dispersing agent, 0.3 parts of substrate wetting agent,
[0049] 0.4 parts of anti-settling agent, 0.4 parts of defoamer,
[0050] 0.3 parts of thickener, 0.3 parts of leveling agent;
[0051] Described component B is composed as follows by weight and number ratio:
[0052] 12 parts of isocyanates, 13 parts of dipropylene glycol dimethyl ether ;
[0053] The functional filler components described in it are the same as those in Example 1.
PUM
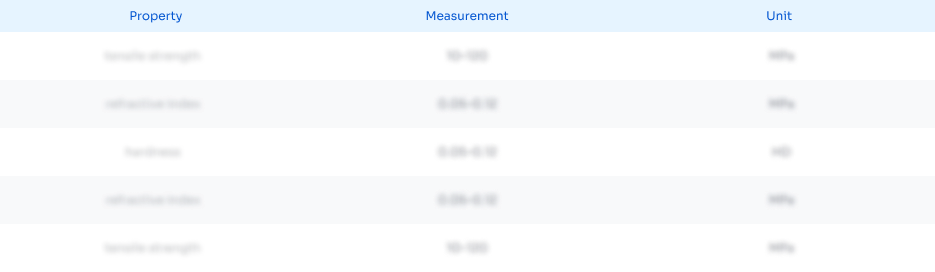
Abstract
Description
Claims
Application Information

- Generate Ideas
- Intellectual Property
- Life Sciences
- Materials
- Tech Scout
- Unparalleled Data Quality
- Higher Quality Content
- 60% Fewer Hallucinations
Browse by: Latest US Patents, China's latest patents, Technical Efficacy Thesaurus, Application Domain, Technology Topic, Popular Technical Reports.
© 2025 PatSnap. All rights reserved.Legal|Privacy policy|Modern Slavery Act Transparency Statement|Sitemap|About US| Contact US: help@patsnap.com