Method for manufacturing red clay flambe-glazed pottery product
A manufacturing method and kiln-changing glaze technology, which is applied in the field of ceramic products, can solve the problems of low firing cost, high cost of two or even three firings, etc., and achieve the effect of low cost
- Summary
- Abstract
- Description
- Claims
- Application Information
AI Technical Summary
Problems solved by technology
Method used
Examples
Embodiment
[0023] Embodiment 1 The manufacture method of low-temperature laterite kiln glazed pottery
[0024] Including the following steps:
[0025] Step 1, making the bottom glaze: mix the following raw materials in parts by weight: 46 parts of frit, 13 parts of feldspar, 6 parts of light calcium, 7 parts of kaolin, 3 parts of zinc oxide, 2 parts of barium carbonate, 2 parts of zirconium silicate, 4 parts of copper oxide and 4 parts of titanium oxide, after mixing, add 8 parts of waste glass, then add a certain amount of water to mix, put it into a ball mill and grind it into a glaze slurry, and then add 4 parts of low-expansion glaze powder to the glaze slurry to make bottom glaze;
[0026] Step 2: Make the surface glaze: mix the following raw materials in parts by weight: 33 parts of frit, 8 parts of feldspar, 4 parts of kaolin, 13 parts of iron oxide, 10 parts of zirconia, 8 parts of flux, 10 parts of zinc oxide, mix Finally, add 8 parts of waste glass, then add a certain amount ...
Embodiment 2
[0030] Embodiment 2 The manufacturing method of medium-temperature laterite kiln glazed pottery
[0031] Including the following steps:
[0032] Step 1, making the bottom glaze: mix the following raw materials in parts by weight: 50 parts of frit, 15 parts of feldspar, 7 parts of light calcium, 8 parts of kaolin, 4 parts of zinc oxide, 3 parts of barium carbonate, 3 parts of zirconium silicate, 5 parts of copper oxide and 5 parts of titanium oxide, after mixing, add 5 parts of waste glass, then add a certain amount of water to mix, put it into a ball mill and grind it into a glaze slurry, and then add 1.5 parts of low expansion glaze powder to the glaze slurry to make bottom glaze;
[0033] Step 2: Make the surface glaze: mix the following raw materials in parts by weight: 37 parts of frit, 10 parts of feldspar, 5 parts of kaolin, 15 parts of iron oxide, 11 parts of zirconia, 10 parts of flux, 12 parts of zinc oxide, mix Finally, add 5 parts of waste glass, then add a certai...
Embodiment 3
[0037] Embodiment 3 The manufacture method of high-temperature laterite kiln glazed pottery
[0038] Including the following steps:
[0039] Step 1, making the bottom glaze: mix the following raw materials in parts by weight: 54 parts of frit, 17 parts of feldspar, 8 parts of light calcium, 10 parts of kaolin, 5 parts of zinc oxide, 4 parts of barium carbonate, 4 parts of zirconium silicate, 6 parts of copper oxide and 6 parts of titanium oxide, after mixing, add 3 parts of waste glass, then add a certain amount of water to mix, put it into a ball mill and grind it into a glaze slurry to obtain a bottom glaze;
[0040] Step 2: Make the surface glaze: mix the following raw materials in parts by weight: 42 parts of frit, 12 parts of feldspar, 6 parts of kaolin, 18 parts of iron oxide, 12 parts of zirconia, 12 parts of flux, 15 parts of zinc oxide, mix Finally, add 3 parts of waste glass, then add a certain amount of water and mix well, then put it into a ball mill and grind it ...
PUM
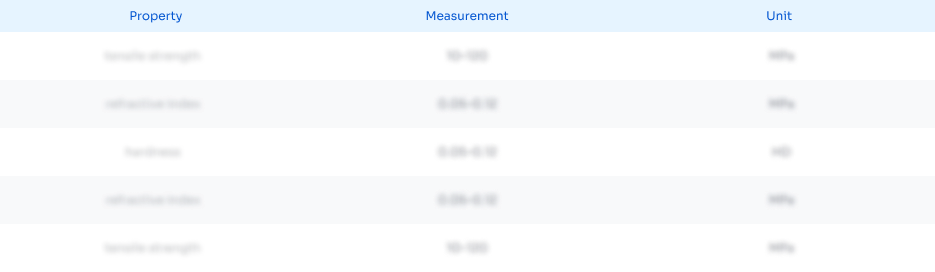
Abstract
Description
Claims
Application Information

- R&D Engineer
- R&D Manager
- IP Professional
- Industry Leading Data Capabilities
- Powerful AI technology
- Patent DNA Extraction
Browse by: Latest US Patents, China's latest patents, Technical Efficacy Thesaurus, Application Domain, Technology Topic, Popular Technical Reports.
© 2024 PatSnap. All rights reserved.Legal|Privacy policy|Modern Slavery Act Transparency Statement|Sitemap|About US| Contact US: help@patsnap.com