Preparation and application methods of thermoplastic adhesive for powder microinjection molding
A thermoplastic binder and binder technology are applied in the field of preparation and removal of thermoplastic binders for metal and ceramic powder micro-injection molding, which can solve the problems of insufficient feeding fluidity and incomplete filling. Achieve the effect of expanding the scope of production and application, high dimensional and shape accuracy, and improved forming accuracy
- Summary
- Abstract
- Description
- Claims
- Application Information
AI Technical Summary
Problems solved by technology
Method used
Image
Examples
Embodiment 1
[0018] The composition of the binder is: 36%PW + 9%BW + 25%HDPE + 20%EVA + 10%SA, where each component is a mass percentage. The process is: in a constant temperature device, at a temperature of 110 oC, high-density polyethylene is first added and melted, and then ethylene-vinyl acetate, paraffin wax, beeswax, and stearic acid are added in sequence. After all the components are melted, continue heating and stirring for 10 minutes, and mix thoroughly to obtain a premixed binder. The volume ratio of binder to metal powder is 54:46 ratio , Add the solid powder in 3 times on average until all are mixed evenly. The mixing time of powder and binder is 1.5 hours. The injection temperature of the feed is 145-160oC, and the injection pressure is 60-80MPa. After the injection, solvent degreasing + thermal degreasing is used to remove the binder. Among them, the process of solvent degreasing is soaked for 6 hours, and the solvent is carbon tetrachloride.
Embodiment 2
[0020] The composition of the binder is: 30%PW + 12%BW + 32%HDPE + 18%EVA + 8%SA, where each component is a mass percentage. The process is: in a constant temperature device, at a temperature of 130 oC, high-density polyethylene is first added and melted, and then ethylene-vinyl acetate, paraffin wax, beeswax, and stearic acid are added in sequence. After all the components are melted, continue heating and stirring for 10 minutes, and mix thoroughly to obtain a premixed binder. The volume ratio of the binder and the metal powder is 46:54, and the metal or ceramic powder is added in 3 times on average until all are mixed evenly. The mixing time of metal powder and binder is 2 hours. The injection temperature of the feed is 150-165oC, and the injection pressure is 70-90MPa. After the injection is completed, solvent degreasing + thermal degreasing is used to remove the binder. Among them, the process of solvent degreasing is soaked for 12 hours, and the solvent is n-heptane.
Embodiment 3
[0022] The composition of the binder is: 20%PW + 15%BW + 20%HDPE + 30%EVA + 15%SA, where each component is a mass percentage. The process is as follows: in a constant temperature device, at a temperature of 150 oC, high-density polyethylene is first added and melted, and then ethylene-vinyl acetate, paraffin wax, beeswax, and stearic acid are added in sequence. After all the components are melted, continue heating and stirring for 10 minutes, and mix thoroughly to obtain a premixed binder. The volume ratio of binder and ceramic powder is 50:50 ratio, Add the ceramic powder in 3 times on average until all are mixed evenly. The mixing time of ceramic powder and binder is 2 hours. The injection temperature of the feed is 145-165oC, and the injection pressure is 60-90MPa. After the injection is complete, the binder is removed by thermal degreasing.
PUM
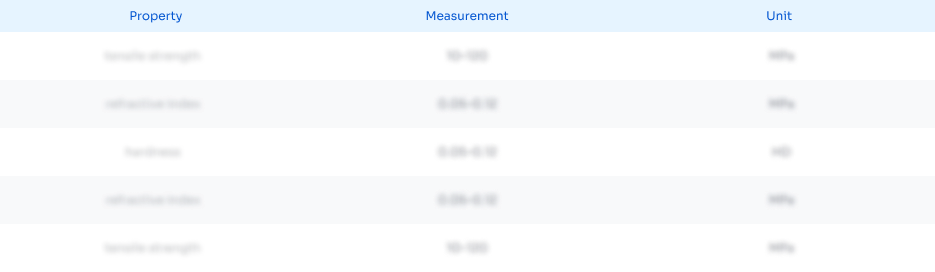
Abstract
Description
Claims
Application Information

- R&D Engineer
- R&D Manager
- IP Professional
- Industry Leading Data Capabilities
- Powerful AI technology
- Patent DNA Extraction
Browse by: Latest US Patents, China's latest patents, Technical Efficacy Thesaurus, Application Domain, Technology Topic, Popular Technical Reports.
© 2024 PatSnap. All rights reserved.Legal|Privacy policy|Modern Slavery Act Transparency Statement|Sitemap|About US| Contact US: help@patsnap.com