Large-area welding method
A welding method and large-area technology, applied in the field of microelectronics, can solve problems such as welding failure, and achieve the effect of improving welding quality
- Summary
- Abstract
- Description
- Claims
- Application Information
AI Technical Summary
Problems solved by technology
Method used
Image
Examples
Embodiment Construction
[0018] In order to solve the surface error problem of the welding surface in the prior art, the present invention provides a large-area welding method. The present invention will be further described in detail below with reference to the accompanying drawings and embodiments. It should be understood that the specific embodiments described here are only used to explain the present invention, not to limit the present invention.
[0019] figure 1 It is a flow chart of the large-area welding method of the present invention. The embodiment of the present invention relates to a large-area welding method, specifically:
[0020] Firstly, welding films are respectively made on the welding surfaces of the two welding pieces to be welded. The welding film is a metal material layer covering the welding surface. The present invention uses two metals with different melting points to make the welding film, wherein the welding film with a high melting point has a microstructure with an indep...
PUM
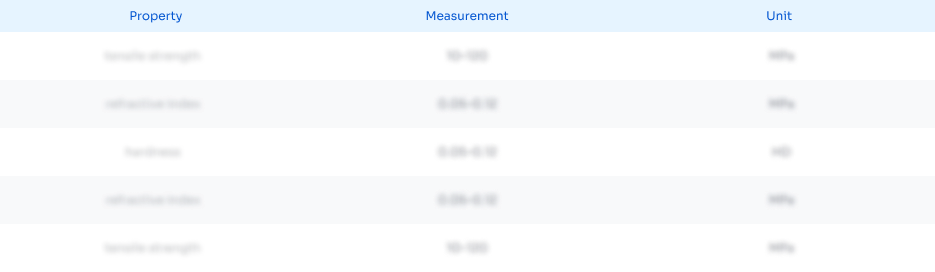
Abstract
Description
Claims
Application Information

- R&D Engineer
- R&D Manager
- IP Professional
- Industry Leading Data Capabilities
- Powerful AI technology
- Patent DNA Extraction
Browse by: Latest US Patents, China's latest patents, Technical Efficacy Thesaurus, Application Domain, Technology Topic, Popular Technical Reports.
© 2024 PatSnap. All rights reserved.Legal|Privacy policy|Modern Slavery Act Transparency Statement|Sitemap|About US| Contact US: help@patsnap.com