Titanium-silicalite molecular sieve, method for preparing the same and method for preparing cyclohexanone oxime using the molecular sieve
A technology of silicon molecular sieve and cyclohexanone oxime, which is applied in the direction of molecular sieve catalysts, molecular sieve characteristic silicates, molecular sieves and alkali exchange compounds, etc., can solve the limitation of use efficiency, complicated and lengthy synthesis steps, and the inability to increase the efficiency of hydrogen peroxide and increase the manufacturing cost and other problems, to achieve the effect of high hydrogen peroxide usage rate, high conversion rate and selectivity
- Summary
- Abstract
- Description
- Claims
- Application Information
AI Technical Summary
Problems solved by technology
Method used
Image
Examples
Embodiment 1
[0030] Preparation of V-TS-1 (catalyst A)
[0031]Put a 500ml round-bottomed flask under nitrogen blanketing in a vacuum system, take 1.932 grams of tetra-n-butyl titanate and add it into the nitrogen-filled round-bottomed flask and cool the temperature to 5°C. After the temperature is balanced, take 30.27 grams of tetraethylsilicate Add dropwise, stir after 1 hour and get 56.5 grams (content 20wt%) tetra-n-propyl ammonium hydroxide isopropanol solution and add dropwise, get the hydrated vanadyl sulfate of 0.19g after finishing and be dissolved in the water of 20 milliliters, this Add the vanadium source aqueous solution drop by drop, stir evenly, remove alcohol at 85°C and add water until the total weight is 100g to complete the colloidal mixture. Seal the colloidal mixture in a hydrothermal tank, heat it at 180°C for 120 hours, separate the solid from the liquid, wash the solid part with water until neutral, dry at 100°C and calcinate at 550°C for 8 hours to produce the cata...
Embodiment 2
[0033] Preparation of Fe-TS-1 (catalyst B)
[0034] Put a 500ml round-bottomed flask in a vacuum system for nitrogen blanketing, take 1.98 grams of tetra-n-butyl titanate and add it into the nitrogen-packed round-bottomed flask and cool the temperature to 5°C. After the temperature is balanced, take 30 grams of tetraethylsilicate Add dropwise, stir after 1 hour and get 56 grams (content 20wt%) tetra-n-propylammonium hydroxide isopropanol solution and add dropwise, get 0.39g iron trichloride hexahydrate and be dissolved in the water of 20 milliliters after finishing, Add the iron source aqueous solution dropwise, stir evenly, remove alcohol at 85°C, and then add water until the total weight is 100g to complete the colloidal mixture. Enclose the colloidal mixture in a hydrothermal tank, heat it at 180°C for 120 hours, separate the solid from the liquid, wash the solid part with water until neutral, dry at 100°C and calcinate at 550°C for 8 hours to produce the catalyst. Its X-R...
Embodiment 3
[0036] Preparation of Co-TS-1 (catalyst C)
[0037] Put a 500ml round-bottomed flask in a vacuum system for nitrogen blanketing, take 1.98 grams of tetra-n-butyl titanate and add it into the nitrogen-packed round-bottomed flask and cool the temperature to 5°C. After the temperature is balanced, take 30 grams of tetraethylsilicate Add dropwise, after stirring for 1 hour, get 56 grams (content 20wt%) of tetra-n-propylammonium hydroxide isopropanol solution and add dropwise, after completion, get 0.0143g cobalt acetate tetrahydrate and dissolve it in 20 milliliters of water. Add the cobalt source aqueous solution dropwise, stir evenly, remove alcohol at 85°C, and then add water to a total weight of 100g to complete the colloidal mixture. Seal the colloidal mixture in a hydrothermal tank, heat it at 180°C for 120 hours, separate the solid from the liquid, wash the solid part with water until neutral, dry at 100°C and calcinate at 550°C for 8 hours to produce the catalyst.
PUM
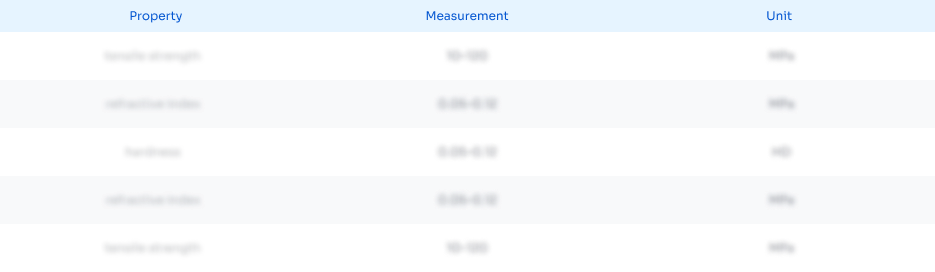
Abstract
Description
Claims
Application Information

- R&D Engineer
- R&D Manager
- IP Professional
- Industry Leading Data Capabilities
- Powerful AI technology
- Patent DNA Extraction
Browse by: Latest US Patents, China's latest patents, Technical Efficacy Thesaurus, Application Domain, Technology Topic, Popular Technical Reports.
© 2024 PatSnap. All rights reserved.Legal|Privacy policy|Modern Slavery Act Transparency Statement|Sitemap|About US| Contact US: help@patsnap.com