Method for preparing 2,6-dimethylnaphthalene by catalyzing naphthalene alkylation reaction with CoAPO-11 molecular sieve
A technology for catalyzing naphthalene and alkylation reactions with molecular sieves, applied in molecular sieve catalysts, chemical instruments and methods, physical/chemical process catalysts, etc., can solve the problems of not being able to have high activity at the same time, and achieve good redox performance and high catalytic activity , Ease of mass production
- Summary
- Abstract
- Description
- Claims
- Application Information
AI Technical Summary
Problems solved by technology
Method used
Image
Examples
specific Embodiment approach 1
[0020] Specific embodiment one: a kind of CoAPO-11 molecular sieve of this embodiment catalyzes the alkylation reaction of naphthalene to prepare the method for 2,6-dimethylnaphthalene is carried out according to the following steps: one, CoAPO-11 molecular sieve is put into fixed The catalyst bed of the bed reactor is activated at 550°C for 2 hours; 2. Mix naphthalene, alkylating agent and solvent evenly to obtain the raw material liquid, and inject the raw material liquid into the catalyst of the fixed-bed reactor in step 1 with a metering pump Bed, at a temperature of 350°C~450°C, a pressure of 2~5MPa, and a mass space velocity of 0.5~2h -1 , under the condition that the carrier gas flow rate is 20~60mL / min, carry out the alkylation reaction for 6~24h to obtain 2,6-dimethylnaphthalene; wherein, the molar ratio of naphthalene to alkylation reagent is 1:(2 ~4), the mol ratio of naphthalene and solvent is 1:(6~12).
[0021] The present embodiment adopts CoAPO-n molecular siev...
specific Embodiment approach 2
[0022] Specific embodiment two: the difference between this embodiment and specific embodiment one is that the CoAPO-11 molecular sieve described in step one is synthesized by electric heating method, and the specific steps are: pseudoboehmite, cobalt source, mass The percentage content is 85% phosphoric acid, di-n-propylamine and deionized water according to the mass ratio of 5.7: (0.2~0.6): 7.8:3.5: (22.1~26.2) after stirring evenly to make a gel, the gel will be installed Put the polytetrafluoroethylene lining of the glue into the stainless steel outer lining, and then put it in an oven at 180 ° C for 48 hours of crystallization to obtain a solid-liquid mixture; then wash the solid phase obtained by filtration, and put it in a temperature of Dry it in an oven at 110°C for 12h, then put it into a muffle furnace at 650°C and bake it for 7h to get CoAPO-11 molecular sieve; the cobalt source is Co(CH 3 COO) 2 4H 2 O or Co (NO 3 ) 2 ·6H 2 O. Others are the same as in the f...
specific Embodiment approach 3
[0023] Specific embodiment three: the difference between this embodiment and specific embodiment one or two is that the CoAPO-11 molecular sieve described in step one is synthesized by microwave radiation heating, and the specific steps are: pseudoboehmite, cobalt source , the mass percentage content is 85% phosphoric acid, di-n-propylamine, and deionized water according to the mass ratio of 5.7: (0.2~0.6):7.8:3.5: (22.1~26.2) and stir evenly to make a gel, then put the Put the polytetrafluoroethylene lining with gel into the ceramic outer lining, then put it into a microwave oven, and crystallize it for 3 hours at a power of 600W and a temperature of 160-180°C to obtain a solid-liquid mixture; then put After washing the solid phase obtained by filtration, put it into an oven with a temperature of 110° C. to dry for 12 hours, and then put it into a muffle furnace with a temperature of 650° C. and roast it for 7 hours to obtain CoAPO-11 molecular sieve; wherein the cobalt source...
PUM
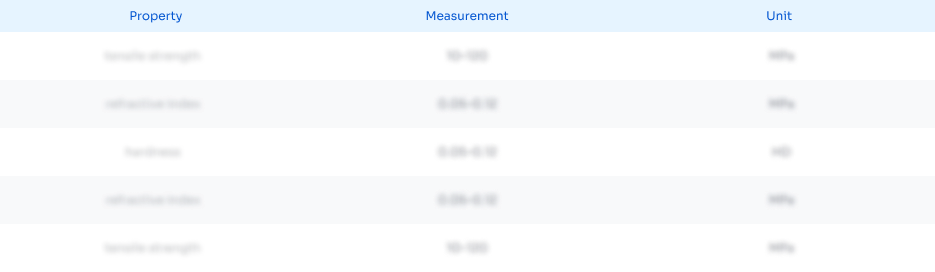
Abstract
Description
Claims
Application Information

- R&D
- Intellectual Property
- Life Sciences
- Materials
- Tech Scout
- Unparalleled Data Quality
- Higher Quality Content
- 60% Fewer Hallucinations
Browse by: Latest US Patents, China's latest patents, Technical Efficacy Thesaurus, Application Domain, Technology Topic, Popular Technical Reports.
© 2025 PatSnap. All rights reserved.Legal|Privacy policy|Modern Slavery Act Transparency Statement|Sitemap|About US| Contact US: help@patsnap.com