Novel erosion resistant cupronickel alloy and preparation method thereof
A corrosion-resistant, cupronickel technology, applied in the field of corrosion-resistant cupronickel alloy and its preparation, can solve the problems of high price and restrict the use of B30 alloy, and achieve the effect of reducing production difficulty, improving mechanical properties and corrosion resistance, and simplifying the preparation process
- Summary
- Abstract
- Description
- Claims
- Application Information
AI Technical Summary
Problems solved by technology
Method used
Image
Examples
Embodiment 1
[0025] The alloy of the present invention adopts the following raw materials for smelting: electrolytic copper, pure nickel, copper iron, copper manganese and copper yttrium intermediate alloy, pure tin. The composition of the alloy is shown in Example 1 of Table 1.
[0026] 1. Melting: use non-vacuum induction furnace for melting. The order of adding the alloy is: first add electrolytic copper, pure nickel, copper-iron intermediate alloy, copper-manganese intermediate alloy, raise the temperature to 1250°C, and after the melt is completely melted, cover it with charcoal and keep it warm for 10 minutes, then add pure tin and copper Yttrium master alloy, then covered with burning charcoal. The converter is poured into the holding furnace. After fully stirring and degassing, stand still for 5 minutes and cast out of the furnace. The casting temperature is 1150°C, the outlet temperature of the ingot is 320°C, and the outlet water temperature is 50°C.
[0027] 2. Face milling: ...
Embodiment 2
[0035] The alloy of the present invention adopts the following raw materials for smelting: electrolytic copper, pure nickel, copper iron, copper manganese and copper yttrium intermediate alloy, pure tin. The composition of the alloy is shown in Example 2 of Table 1.
[0036] 1. Melting: use non-vacuum induction furnace for melting. The order of adding the alloys is: electrolytic copper, pure nickel, copper-iron master alloy, copper-manganese master alloy, raise the temperature to 1270°C until the melt is completely melted, cover with charcoal, keep warm for 10min, add pure tin and copper yttrium Alloy, then covered with burning charcoal. The converter is poured into the holding furnace. After fully stirring and degassing, stand still for 5 minutes and cast out of the furnace. The casting temperature is 1170°C, the outlet temperature of the ingot is 340°C, and the outlet water temperature is 52°C.
[0037] 2. Face milling: Milling the alloy, milling 1mm on the upper and lowe...
Embodiment 3
[0045] The alloy of the present invention adopts the following raw materials for smelting: electrolytic copper, pure nickel, copper iron, copper manganese and copper yttrium intermediate alloy, pure tin. The composition of the alloy is shown in Example 3 of Table 1.
[0046] 1. Melting: use non-vacuum induction furnace for melting. The order of adding the alloys is: electrolytic copper, pure nickel, copper-iron master alloy, copper-manganese master alloy, raise the temperature to 1260°C, until the melt is completely melted, cover with charcoal, keep warm for 10min, add pure tin and copper yttrium Alloy, then covered with burning charcoal. The converter is poured into the holding furnace. After fully stirring and degassing, stand still for 5 minutes and cast out of the furnace. The casting temperature is 11-80°C, the outlet temperature of the ingot is 350°C, and the outlet water temperature is 55°C.
[0047] 2. Face milling: Milling the alloy, milling 1mm on the upper and lo...
PUM
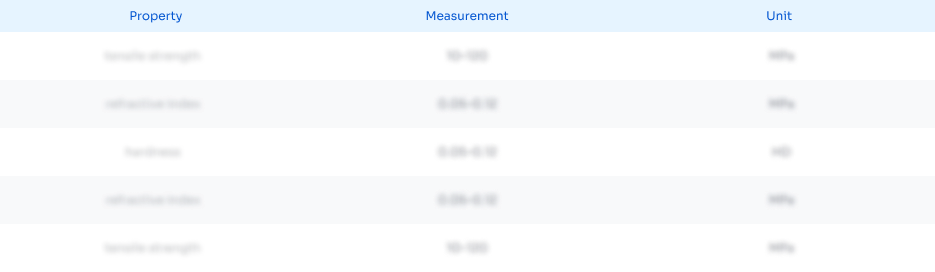
Abstract
Description
Claims
Application Information

- R&D
- Intellectual Property
- Life Sciences
- Materials
- Tech Scout
- Unparalleled Data Quality
- Higher Quality Content
- 60% Fewer Hallucinations
Browse by: Latest US Patents, China's latest patents, Technical Efficacy Thesaurus, Application Domain, Technology Topic, Popular Technical Reports.
© 2025 PatSnap. All rights reserved.Legal|Privacy policy|Modern Slavery Act Transparency Statement|Sitemap|About US| Contact US: help@patsnap.com