A kind of ptc core material with positive temperature coefficient characteristic and its manufacture and application
A positive temperature coefficient, core material technology, applied in the direction of resistors with positive temperature coefficients, current response resistors, etc., can solve the problems that affect the metal foil electrode coating effect, reduce the electrical performance of the product, etc., and meet the requirements of the preparation Effects of short time, increased production speed, and increased resistance reproducibility
- Summary
- Abstract
- Description
- Claims
- Application Information
AI Technical Summary
Problems solved by technology
Method used
Image
Examples
Embodiment 1
[0047] The formula of the present embodiment is as shown in Table 1 and Table 2. The difference from the comparative example is that the peroxide is added during the plasticization of the open mill, and the volume percentage of the peroxide is 2%, and then stretched to a length of 20 cm and a width of 10 cm. , after cooling, put it into a mold with a middle thickness of 0.35-0.37mm, place a nickel foil on the upper and lower surfaces of the PTC plate, then place a polyester film cloth on the upper and lower layers, and then press the steel plate, preheat for 5 minutes, and then press for 10 minutes, the operating pressure is 100kg / cm 2 , the temperature is 160°C, and a PTC core material with positive temperature coefficient characteristics is formed after this first pressing. Then the PTC core material is cut into a rectangle with a length of 20 cm and a width of 10 cm, and then punched into a chip with a length of 4 mm and a width of 3 mm by a punching machine, and then welds...
Embodiment 2
[0049] The formula of this embodiment is shown in Table 1 and Table 2. The difference from the comparative example is that peroxide is added during plasticization of the open mill, and its volume percentage is 2%, and then drawn into 10*20mm 2 Thin sheet, after cooling, put it into a mold with a middle thickness of 0.35-0.37mm, put a nickel foil on the upper and lower surfaces of the PTC sheet, and then put a polyester film cloth on the upper and lower layers, and then press the steel plate, preheat for 5 minutes, and then press together 10 minutes, the operating pressure is 100kg / cm 2 , the temperature is 170°C, and a PTC core material with positive temperature coefficient characteristics is formed after the first pressing. Then the PTC core material is cut into a rectangle with a length of 20 cm and a width of 10 cm, and then punched into a chip with an area of 4 mm and a width of 3 mm with a mold, and then welding pins with a length of 16 mm and a width of 2.5 mm and a th...
Embodiment 3
[0051] The formula of the present embodiment is as shown in Table 1 and Table 2. The difference with the comparative example is that the peroxide is added during the plasticization of the open mill, and its volume percentage is 4%, and then stretched into a long 20cm wide 10cm sheet, After cooling, put it into a mold with a middle thickness of 0.35-0.37mm. Put a nickel foil on the upper and lower surfaces of the PTC plate, and then put a polyester film cloth on the upper and lower layers, and then press the steel plate. Preheat for 5 minutes, and then press for 10 minutes. , the operating pressure is 100kg / cm 2 , the temperature is 160°C, and a PTC core material with positive temperature coefficient characteristics is formed after this first pressing. Then the PTC core material is cut into a rectangle with a length of 20cm and a width of 10cm, and then punched into a chip with an area of 4mm and a width of 3mm with a mold, and then welding pins at both ends of the chip with ...
PUM
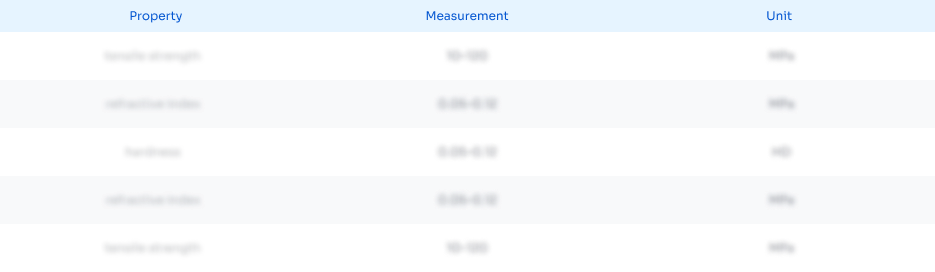
Abstract
Description
Claims
Application Information

- R&D Engineer
- R&D Manager
- IP Professional
- Industry Leading Data Capabilities
- Powerful AI technology
- Patent DNA Extraction
Browse by: Latest US Patents, China's latest patents, Technical Efficacy Thesaurus, Application Domain, Technology Topic, Popular Technical Reports.
© 2024 PatSnap. All rights reserved.Legal|Privacy policy|Modern Slavery Act Transparency Statement|Sitemap|About US| Contact US: help@patsnap.com