Method for producing ultra-low carbon high-strength cold rolling sheet
A production method and high-strength technology, applied in the field of smelting and rolling technology, can solve the problem of large anisotropy of steel, affecting the service performance of the rolled steel plate, affecting the brittleness of secondary processing, chemical treatment performance, alloying galvanizing adaptability, etc. problem, to achieve high tensile strength, ensure formability and impact resistance
- Summary
- Abstract
- Description
- Claims
- Application Information
AI Technical Summary
Problems solved by technology
Method used
Examples
Embodiment 1
[0021] The production process route of molten iron pretreatment-converter smelting-refining furnace refining-continuous casting-hot rolling-cold rolling-acid rolling-continuous annealing-finishing is adopted. The specific production process and control parameters are:
[0022] 1. The chemical composition and weight percentage (wt%) of steel are:
[0023] C
Si
mn
P
S
als
Ti
Nb
B
0.0058
0.40
0.50
0.06
0.020
0.05
0.08
0.045
0.0010
[0024] 2. Hot rolling process system:
[0025] Billet heating temperature: 1260°C;
[0026] Finishing temperature of hot rolling: 950°C;
[0027] Strip coiling temperature: 650°C.
[0028] 3. Cold rolling process system:
[0029] Cold rolling reduction: 85%;
[0030] Continuous annealing furnace: soaking outlet temperature 810°C, slow cooling outlet temperature: 650°C, fast cooling outlet temperature 410°C, overaging outlet temperature...
Embodiment 2
[0033] The production process route of molten iron pretreatment-converter smelting-refining furnace refining-continuous casting-hot rolling-cold rolling-acid rolling-continuous annealing-finishing is adopted. The specific production process and control parameters are:
[0034] 1. The chemical composition and weight percentage (wt%) of steel are:
[0035] C
Si
mn
P
S
als
Ti
Nb
B
0.0050
0.45
1.0
0.08
0.018
0.06
0.05
0.075
0.0006
[0036] 2. Hot rolling process system:
[0037] Billet heating temperature: 1240°C;
[0038] Finishing temperature of hot rolling: 900°C;
[0039] Strip coiling temperature: 610°C.
[0040] 3. Cold rolling process system:
[0041] Cold rolling reduction: 72%;
[0042] Continuous annealing furnace: soaking outlet temperature 840°C, slow cooling outlet temperature: 690°C, fast cooling outlet temperature 430°C, overaging outlet temperature ...
Embodiment 3
[0045] The production process route of molten iron pretreatment-converter smelting-refining furnace refining-continuous casting-hot rolling-cold rolling-acid rolling-continuous annealing-finishing is adopted. The specific production process and control parameters are:
[0046] 1. The chemical composition and weight percentage (wt%) of steel are:
[0047] C
Si
mn
P
S
als
Ti
Nb
B
0.0055
0.50
0.75
0.09
0.022
0.04
0.03
0.035
0.0020
[0048] 2. Hot rolling process system:
[0049] Billet heating temperature: 1210°C;
[0050] Finishing temperature of hot rolling: 890°C;
[0051] Strip coiling temperature: 690°C.
[0052] 3. Cold rolling process system:
[0053] Cold rolling reduction: 78%;
[0054] Continuous annealing furnace: soaking outlet temperature 825°C, slow cooling outlet temperature: 635°C, fast cooling outlet temperature 3900°C, overaging outlet temperatur...
PUM
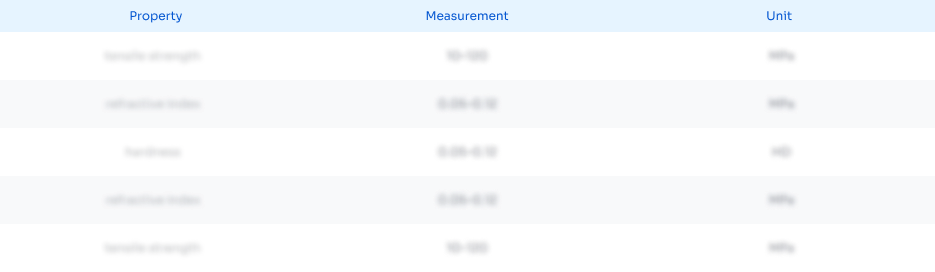
Abstract
Description
Claims
Application Information

- Generate Ideas
- Intellectual Property
- Life Sciences
- Materials
- Tech Scout
- Unparalleled Data Quality
- Higher Quality Content
- 60% Fewer Hallucinations
Browse by: Latest US Patents, China's latest patents, Technical Efficacy Thesaurus, Application Domain, Technology Topic, Popular Technical Reports.
© 2025 PatSnap. All rights reserved.Legal|Privacy policy|Modern Slavery Act Transparency Statement|Sitemap|About US| Contact US: help@patsnap.com