Anti-skid cool foamed floor mat
A non-slip and foam technology, which is applied in the field of foam floor mat products, can solve the problems of affecting quality and easy peeling of product coating, and achieve the effects of improved processing performance, compact structure and increased flexibility
- Summary
- Abstract
- Description
- Claims
- Application Information
AI Technical Summary
Problems solved by technology
Method used
Examples
Embodiment 1
[0022] Material selection:
[0023] The body of the foam floor mat is a non-slip foam floor mat with an integrally formed anti-slip treatment layer:
[0024] Main ingredients EVA: 80 parts by mass, POE: 20 parts by mass, talc powder: 5 parts by mass, AC: 3.5 parts by mass, zinc oxide: 2.5 parts by mass, BIPB: 1.5 parts by mass, stearic acid: 1.5 parts by mass.
[0025] Mix the above components into a banbury mixer for a banburying: the banburying temperature is 115-125°C, the time is 6-8 minutes, and the speed is 985 rpm.
[0026] The second banburying: the banburying temperature is 100-115°C, the time is 4-6 minutes, and the speed is 985 rpm.
[0027] Sheeting and slicing: Put the rubber compound after secondary compaction in the sheeting extruder, extrude it into thin slices with a thickness of 1-2mm at a temperature of 100-110°C, and cut into shapes of equal specifications.
[0028] Lay 4 thin sheets into a foaming mold and foam at a temperature of 170°C for 380-420...
Embodiment 2
[0039] Material selection:
[0040] Ordinary Foam Formula:
[0041] Main ingredients: PE: 100 parts by mass, talc powder: 5 parts by mass, AC: 3.5 parts by mass, zinc oxide: 2.5 parts by mass, BIPB: 1.5 parts by mass, stearic acid: 1.5 parts by mass.
[0042] Non-slip treatment layer formula:
[0043] Main ingredients EVA: 80 parts by mass, POE: 20 parts by mass, talc powder: 5 parts by mass, AC: 3.5 parts by mass, zinc oxide: 2.5 parts by mass, BIPB: 1.5 parts by mass, stearic acid: 1.5 parts by mass.
[0044] Mix the above-mentioned ordinary foam formula components into a banbury mixer for one-time banburying: the banburying temperature is 135-140°C, the time is 8-12 minutes, and the speed is 985 rpm.
[0045] The second banburying: the banburying temperature is 115-125°C, the time is 5-7 minutes, and the speed is 985 rpm.
[0046] Sheeting and slicing: Put the rubber compound after secondary compaction in the sheeting extruder, extrude it into thin slices with a...
PUM
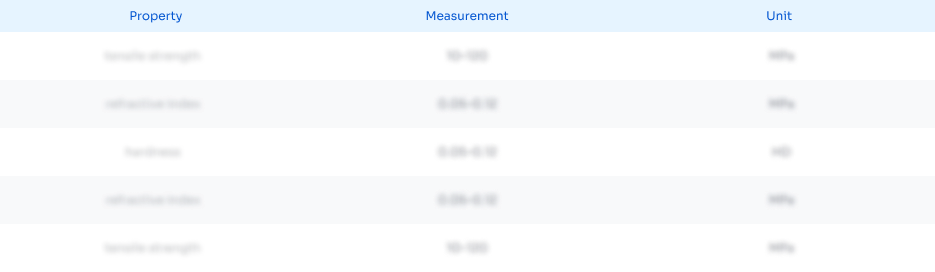
Abstract
Description
Claims
Application Information

- R&D
- Intellectual Property
- Life Sciences
- Materials
- Tech Scout
- Unparalleled Data Quality
- Higher Quality Content
- 60% Fewer Hallucinations
Browse by: Latest US Patents, China's latest patents, Technical Efficacy Thesaurus, Application Domain, Technology Topic, Popular Technical Reports.
© 2025 PatSnap. All rights reserved.Legal|Privacy policy|Modern Slavery Act Transparency Statement|Sitemap|About US| Contact US: help@patsnap.com