Precision casting method for thick-wall base aluminium alloy casting
An aluminum alloy casting and precision casting technology, which is applied in the field of investment precision casting of thick-walled castings, can solve the problems of high one-time forming rate, failing to meet the technical requirements of parts, and high cost, achieving great economic benefits and improving product quality. And the effect of yield and production cost reduction
- Summary
- Abstract
- Description
- Claims
- Application Information
AI Technical Summary
Problems solved by technology
Method used
Examples
Embodiment 1
[0020] 1 Design and manufacture of wax molds: Design and manufacture metal molds according to the structure of the base, the casting shrinkage rate is 1.3, and the draft angle is 2′.
[0021] 2 Press the wax mold: use the wax mold mold made in the first step to press the base wax mold on the wax press machine, the pressing temperature wax cylinder temperature: 60-75 ℃, the nozzle temperature: 60-65 ℃, the mold temperature: 30-35 ℃, injection pressure: 1-3MPa, clamping pressure: 10-15MPa, holding time: 15-25 minutes.
[0022] 3. Design and manufacture of gating system: using a wax press machine to respectively press the sprue cup, runner, sprue and ingate;
[0023] 4. Model repair: remove burrs, drape seams, parting lines, fill pits, pores, shrinkage and other defects, to ensure that the surface of the wax model is smooth and smooth, and the transfer is smooth.
[0024] 5-group type: Use group-type wax to bond the wax mold pressed in the second part and the sprue cup, runner, ...
Embodiment 2
[0038] 1 Design and manufacture of wax molds: Design and manufacture metal molds according to the structure of the base, the casting shrinkage rate is 1.3, and the draft angle is 2′.
[0039] 2 Press the wax mold: use the wax mold mold made in the first step to press the base wax mold on the wax press machine, the pressing temperature wax cylinder temperature: 60-75 ℃, the nozzle temperature: 60-65 ℃, the mold temperature: 30-35 ℃, injection pressure: 1-3MPa, clamping pressure: 10-15MPa, holding time: 15-25 minutes.
[0040] 3. Design and manufacture of gating system: using a wax press machine to respectively press the sprue cup, runner, sprue and ingate;
[0041] 4. Model repair: remove burrs, drape seams, parting lines, fill pits, pores, shrinkage and other defects, to ensure that the surface of the wax model is smooth and smooth, and the transfer is smooth.
[0042] 5-group type: Use group-type wax to bond the wax mold pressed in the second part and the sprue cup, runner, ...
Embodiment 3
[0056] 1 Design and manufacture of wax molds: Design and manufacture metal molds according to the structure of the base, the casting shrinkage rate is 1.3, and the draft angle is 2′.
[0057] 2 Press the wax mold: use the wax mold mold made in the first step to press the base wax mold on the wax press machine, the pressing temperature wax cylinder temperature: 60-75 ℃, the nozzle temperature: 60-65 ℃, the mold temperature: 30-35 ℃, injection pressure: 1-3MPa, clamping pressure: 10-15MPa, holding time: 15-25 minutes.
[0058] 3. Design and manufacture of gating system: using a wax press machine to respectively press the sprue cup, runner, sprue and ingate;
[0059] 4. Model repair: remove burrs, drape seams, parting lines, fill pits, pores, shrinkage and other defects, to ensure that the surface of the wax model is smooth and smooth, and the transfer is smooth.
[0060] 5-group type: Use group-type wax to bond the wax mold pressed in the second part and the sprue cup, runner, ...
PUM
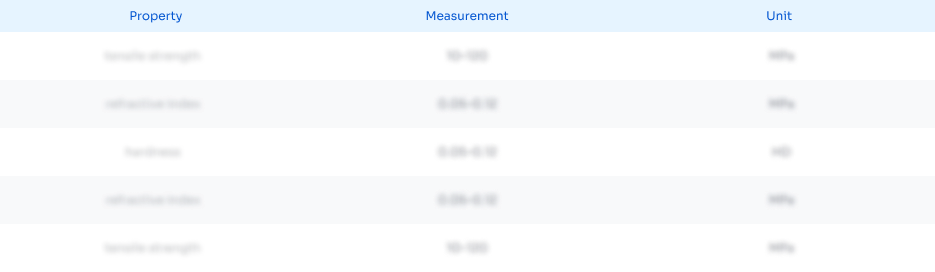
Abstract
Description
Claims
Application Information

- R&D
- Intellectual Property
- Life Sciences
- Materials
- Tech Scout
- Unparalleled Data Quality
- Higher Quality Content
- 60% Fewer Hallucinations
Browse by: Latest US Patents, China's latest patents, Technical Efficacy Thesaurus, Application Domain, Technology Topic, Popular Technical Reports.
© 2025 PatSnap. All rights reserved.Legal|Privacy policy|Modern Slavery Act Transparency Statement|Sitemap|About US| Contact US: help@patsnap.com