High-performance magnesium alloy welding active agent
A technology of activator and magnesium alloy, which is applied in welding equipment, welding medium, welding equipment, etc., can solve problems such as the decrease of molten pool temperature gradient, adverse effects on welded joint structure and performance, and poor thermal conductivity of activator
- Summary
- Abstract
- Description
- Claims
- Application Information
AI Technical Summary
Problems solved by technology
Method used
Image
Examples
example 1
[0018] Active agent weight ratio is MnCl 2 : 70% and ZnO: 30%. MnCl 2 and ZnO active agent powder are fully ground and mixed in proportion, and then acetone is added to the mixture to make it into a paste. Then use a flat brush to evenly coat the pasty active agent on the upper surface of the sample, the coating width is about 40 mm, and the average coating amount of the active agent is 6 mg cm -2 . Solder after the acetone evaporates.
[0019] The welding specifications adopted for TIG welding of AZ31 magnesium alloy plates with a plate thickness of 6 mm are as follows:
[0020]
[0021] Under such welding specification conditions, the weld width decreases after coating the compound active agent, and the corrugation of the weld surface is fine and smooth ( Figure 1-3 ). The penetration depth of the weld coated with compound activator is 62.5% higher than that of the weld without activator, and 30% higher than that of the weld coated with single activator ( Figure ...
example 2
[0023] Active agent weight ratio is MnCl 2 : 65% and CaF 2 : ZnO. MnCl 2 and ZnO active agent powder are fully ground and mixed in proportion, and then acetone is added to the mixture to make it into a paste. Then use a flat brush to evenly coat the pasty active agent on the upper surface of the sample, the coating width is about 40 mm, and the average coating amount of the active agent is 6 mg cm -2 . After the acetone volatilizes, perform welding; the welding parameters are the same as in Example 1.
example 3
[0025] Active agent weight ratio is MnCl 2 : 75% and ZnO: 25%. MnCl 2 and ZnO active agent powder are fully ground and mixed in proportion, and then acetone is added to the mixture to make it into a paste. Then use a flat brush to evenly coat the pasty active agent on the upper surface of the sample, the coating width is about 40 mm, and the average coating amount of the active agent is 6 mg cm -2 . After the acetone volatilizes, perform welding; the welding parameters are the same as in Example 1.
PUM
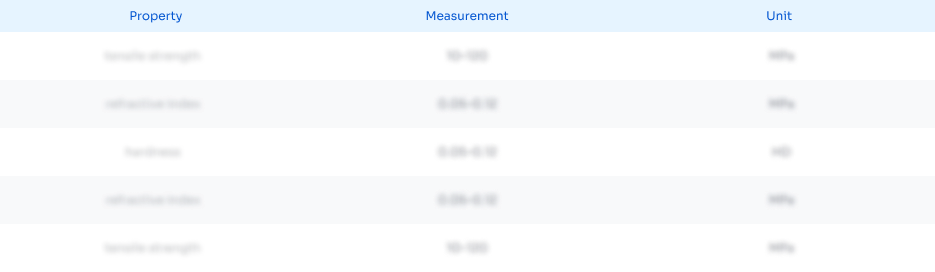
Abstract
Description
Claims
Application Information

- R&D
- Intellectual Property
- Life Sciences
- Materials
- Tech Scout
- Unparalleled Data Quality
- Higher Quality Content
- 60% Fewer Hallucinations
Browse by: Latest US Patents, China's latest patents, Technical Efficacy Thesaurus, Application Domain, Technology Topic, Popular Technical Reports.
© 2025 PatSnap. All rights reserved.Legal|Privacy policy|Modern Slavery Act Transparency Statement|Sitemap|About US| Contact US: help@patsnap.com