Ultra-high molecular weight polyethylene composite material for water lubricated bearing
An ultra-high molecular weight, water-lubricated bearing technology, used in bearing components, shafts and bearings, mechanical equipment, etc., can solve the problems of water-lubricated friction coefficient, difficult to form complete water-lubrication, etc., to improve wear resistance, improve water The effect of lubricating friction performance and improving flexibility
- Summary
- Abstract
- Description
- Claims
- Application Information
AI Technical Summary
Problems solved by technology
Method used
Image
Examples
Embodiment 1
[0017] Take 100 parts of ultra-high molecular weight polyethylene with a molecular weight of 3 million, 30 parts of ordinary nitrile rubber, 10 parts of graphite, 10 parts of molybdenum disulfide, 1.5 parts of zinc oxide, 0.3 parts of stearic acid, and 1 part of dicumyl peroxide. Parts, 0.1 part of β-(3,5-di-tert-butyl-4-hydroxyphenyl) octadecyl propionate, 2,2,4-trimethyl-1,2-dihydroquinoline polymer 0.1 part, the above components were mixed uniformly in an internal mixer at 120°C, then the mixture was placed in a mold, and molded at 170°C to obtain the ultra-high molecular weight polyethylene composite material of the present invention.
Embodiment 2
[0019] Take 100 parts of ultra-high molecular weight polyethylene with a molecular weight of 5 million, 10 parts of hydrogenated nitrile rubber, 40 parts of graphite, 1.0 part of zinc oxide, 0.3 part of stearic acid, 1,4-bis-(2-tert-butyl peroxide) 0.1 part of cumene oxide, 0.2 part of β-(3,5-di-tert-butyl-4-hydroxyphenyl) octadecyl propionate, 0.2 part of 1,1,3-tris(2-methyl- 0.3 parts of 4-hydroxy-5-tert-butylphenyl) butane, 0.2 parts of 2,2,4-trimethyl-1,2-dihydroquinoline polymer, the above components were mixed in an internal mixer at 140 ℃, mix evenly, then put the mixture in a mold, and mold it at 190 ℃ to obtain the ultra-high molecular weight polyethylene composite material of the present invention.
Embodiment 3
[0021] Take 100 parts of ultra-high molecular weight polyethylene with a molecular weight of 8 million, 50 parts of carboxylated nitrile rubber, 10 parts of molybdenum disulfide, 5 parts of zinc oxide, 1 part of stearic acid, 1,4-bis-(2-tert-butyl 3 parts of isopropyl peroxide, 1 part of tris(2,4-di-tert-butylphenyl) phosphite, 1 part of 1,1,3-tris(2-methyl-4-hydroxy-5-tert 1 part of butylphenyl)butane, 1 part of 2,2,4-trimethyl-1,2-dihydroquinoline polymer, mix the above components in an internal mixer at 130°C, and then mix the mixture Put it in a mold, and mold it at 180°C to obtain the ultra-high molecular weight polyethylene composite material of the present invention.
PUM
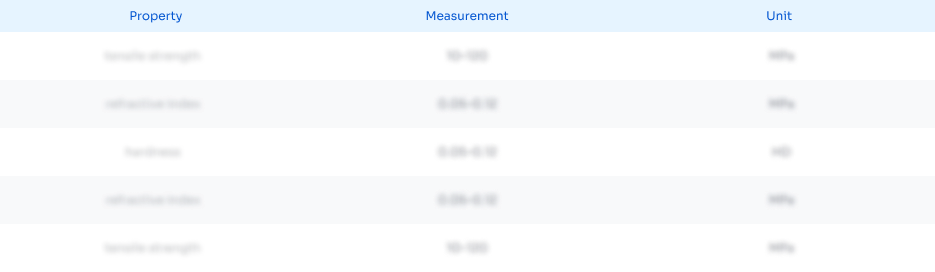
Abstract
Description
Claims
Application Information

- R&D
- Intellectual Property
- Life Sciences
- Materials
- Tech Scout
- Unparalleled Data Quality
- Higher Quality Content
- 60% Fewer Hallucinations
Browse by: Latest US Patents, China's latest patents, Technical Efficacy Thesaurus, Application Domain, Technology Topic, Popular Technical Reports.
© 2025 PatSnap. All rights reserved.Legal|Privacy policy|Modern Slavery Act Transparency Statement|Sitemap|About US| Contact US: help@patsnap.com