Modal testing method of numerical control machine tool feed system based on built-in sensors
A technology of CNC machine tools and feeding systems, which is applied in measuring/indicating equipment, metal processing mechanical parts, metal processing equipment, etc., can solve problems such as differences, achieve high precision and save test costs.
- Summary
- Abstract
- Description
- Claims
- Application Information
AI Technical Summary
Problems solved by technology
Method used
Image
Examples
Embodiment Construction
[0022] The present invention will be described in detail below in conjunction with the accompanying drawings.
[0023] refer to figure 1 , a modal test method for a feed system of a CNC machine tool based on a built-in sensor, comprising the following steps:
[0024] 1) According to the signal types that can be realized by the NC program of the test object, a signal is reasonably selected from the square wave signal, sine wave signal, frequency-swept sine signal, random signal, and pseudo-random signal as the excitation signal, and the excitation signal is determined. Basic parameters, and write the CNC program G code according to the excitation signal, so that the X-axis of the machine tool table moves according to the trajectory of the selected excitation signal;
[0025] 2) While the machine tool table is moving, use multi-channel signal acquisition equipment to simultaneously collect the current of the X-axis servo motor, the encoder of the X-axis servo motor and the sign...
PUM
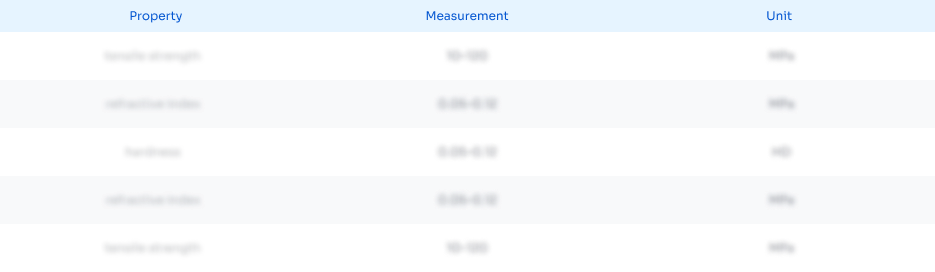
Abstract
Description
Claims
Application Information

- R&D
- Intellectual Property
- Life Sciences
- Materials
- Tech Scout
- Unparalleled Data Quality
- Higher Quality Content
- 60% Fewer Hallucinations
Browse by: Latest US Patents, China's latest patents, Technical Efficacy Thesaurus, Application Domain, Technology Topic, Popular Technical Reports.
© 2025 PatSnap. All rights reserved.Legal|Privacy policy|Modern Slavery Act Transparency Statement|Sitemap|About US| Contact US: help@patsnap.com