Production of carbon nanotube reinforced Fe-based amorphous alloy thermal spray coating and method
A composite technology of iron-based amorphous alloys and carbon nanotubes, which is applied in metal material coating process, coating, melt spraying and other directions, and can solve the non-uniform deformation of iron-based amorphous alloys and the limited application of iron-based amorphous alloys. and other problems to achieve the effect of improving toughness
- Summary
- Abstract
- Description
- Claims
- Application Information
AI Technical Summary
Problems solved by technology
Method used
Image
Examples
Embodiment Construction
[0035] The preparation method of the high-strength and high-toughness iron-based amorphous coating provided by the present invention mainly consists of three steps:
[0036] The preparation process of high-strength and high-toughness iron-based amorphous alloy coating is as follows: figure 1 Shown: First, the iron-based amorphous alloy powder is mixed with multi-walled carbon nanotubes; then, the iron-based amorphous alloy powder and carbon nanotubes are restructured by mechanical ball milling or spray granulation to form a composite Particles; before spraying, the surface of the sprayed base material is roughened by sandblasting; the base material after surface pretreatment is fixed on the workbench; the iron-based amorphous-carbon nanotube composite reconstituted particles are sprayed on the material by thermal spraying technology On the surface, an iron-based amorphous alloy coating is obtained.
[0037] Embodiments of the present invention adopt the following technical co...
PUM
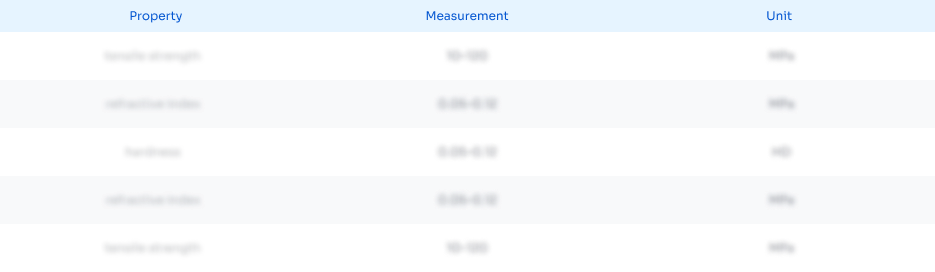
Abstract
Description
Claims
Application Information

- R&D
- Intellectual Property
- Life Sciences
- Materials
- Tech Scout
- Unparalleled Data Quality
- Higher Quality Content
- 60% Fewer Hallucinations
Browse by: Latest US Patents, China's latest patents, Technical Efficacy Thesaurus, Application Domain, Technology Topic, Popular Technical Reports.
© 2025 PatSnap. All rights reserved.Legal|Privacy policy|Modern Slavery Act Transparency Statement|Sitemap|About US| Contact US: help@patsnap.com