Bainite pre-hardening plastic mold steel and preparation method and heat treatment method thereof
A technology of plastic mold steel and pre-hardened type, which is applied in the field of alloy steel manufacturing technology, can solve the problems of long production cycle of quenched and tempered pre-hardened plastic mold steel, lack of international and domestic competitiveness of production enterprises, waste of resources, etc., to save Effect of hydrogen expansion annealing process, shortening production cycle and saving production cost
- Summary
- Abstract
- Description
- Claims
- Application Information
AI Technical Summary
Problems solved by technology
Method used
Image
Examples
Embodiment
[0031] In this example, the composition and weight percentage of the bainite pre-hardened plastic mold steel are as follows:
[0032] C 0.35 % Si 0.34 %
[0033] Mn 2.30 % S 0.005 %
[0034] Cr 1.10% P 0.010%
[0035] Mo 0.12 % Fe balance
[0036] Nb 0.058 %
[0037] In this embodiment, the method and steps of preparing and heat-treating bainitic pre-hardened plastic mold steel are as follows:
[0038] A. Steelmaking: smelting in an electric arc furnace according to the above-mentioned ratio of alloying elements, the smelting temperature is greater than 1500°C, then refining, then vacuum degassing, and finally casting into 25t octagonal steel ingots and air cooling;
[0039] B. Forging: After demolding the above steel ingots, send them to the forging workshop. The surface temperature before entering the furnace is not lower than 500°C, and then adjust the temperature to 1150-1250°C for multi-directional forging processing; forging ratio ≥ 4; opening forging temperature ...
PUM
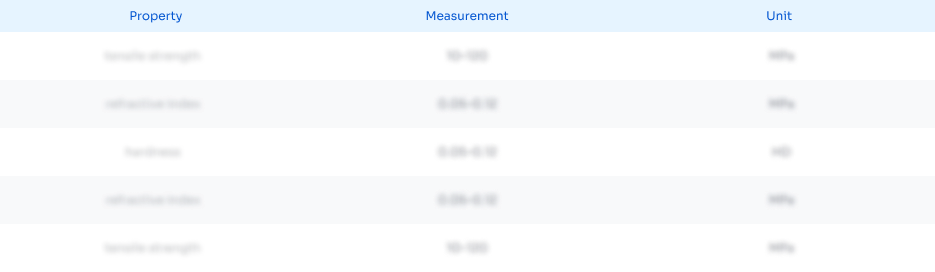
Abstract
Description
Claims
Application Information

- R&D Engineer
- R&D Manager
- IP Professional
- Industry Leading Data Capabilities
- Powerful AI technology
- Patent DNA Extraction
Browse by: Latest US Patents, China's latest patents, Technical Efficacy Thesaurus, Application Domain, Technology Topic, Popular Technical Reports.
© 2024 PatSnap. All rights reserved.Legal|Privacy policy|Modern Slavery Act Transparency Statement|Sitemap|About US| Contact US: help@patsnap.com