Polyurethane reinforced grouting material containing phase change additive and preparation method thereof
A grouting material and additive technology, applied in building insulation materials, building components, buildings, etc., can solve problems such as excessive heat release, and achieve the effect of reducing core temperature, ensuring safety, and excellent sealing and reinforcement performance.
- Summary
- Abstract
- Description
- Claims
- Application Information
AI Technical Summary
Problems solved by technology
Method used
Examples
Embodiment 1
[0021] Weigh polyether polyol, dimethyl methyl phosphate, phase change additive, tin compound, amine compound, reactive solvent 1,4-butanediol and silicone defoamer according to the weight of polyether polyol As a benchmark, dimethyl methyl phosphate is 70%, phase change additive is 80%, tin compound is 2.4%, amine compound is 2.4%, silicone defoamer is 1.0%, 1,4-butanediol 20%, using ultrasound to mix the above raw materials evenly and let it stand for 10 minutes to obtain component A, weigh the isocyanate, control the isocyanate index to 1.05, as component B, add component B to component A, and mix evenly and react at room temperature to finally obtain a polyurethane reinforced grouting material containing phase change additives;
[0022] Wherein the phase change additive described on the basis of polyether polyol weight is: potassium aluminum sulfate dodecahydrate 16.5%, calcium chloride hexahydrate 16.5%, sodium phosphate dodecahydrate 16.8%, calcium sulfate dihydrate 14.8...
Embodiment 2
[0027] Weigh polyether polyol, dimethyl methyl phosphate, phase change additives, tin compounds, amine compounds, reactive solvents and silicone defoamers in proportion, based on polyether polyol, methyl phosphate two Methyl ester is 85%, phase change additive is 50%, tin compound is 2.5%, amine compound is 2.5%, silicone defoamer is 0.5%, 1,4-butanediol is 15%. Mix the above raw materials uniformly and let stand for 15 minutes to obtain component A, weigh the isocyanate, control the isocyanate index to 1.05, as component B, add component B to component A, mix uniformly and react at room temperature, and finally A polyurethane reinforced grouting material containing phase change additives is prepared;
[0028] Wherein with polyether polyol weight as benchmark, described phase change additive is: polyethylene 10.7%, butyl stearate 9.3%, paraffin wax 8.0%, polyisobutylene 11.7%, superfine asphalt 10.3%;
[0029] The catalyst is an amine compound and a tin compound, wherein the ...
Embodiment 3
[0033] Weigh polyether polyol, dimethyl methyl phosphate, phase change additives, tin compounds, amine compounds, reactive solvents and silicone defoamers in proportion, based on polyether polyol, methyl phosphate two Methyl ester is 60%, phase change additive is 12%, tin compound is 2.0%, amine compound is 2.0%, silicone defoamer is 1.5%, 1,4-butanediol is 10%. Mix the above raw materials uniformly and let stand for 20 minutes to obtain component A, weigh the isocyanate, control the isocyanate index to 1.15, as component B, add component B to component A, mix uniformly and react at room temperature, and finally A polyurethane reinforced grouting material containing phase change additives is prepared;
[0034] Wherein based on polyether polyol weight, described phase change additive is: potassium aluminum sulfate dodecahydrate 6.5%, polyethylene 5.5%;
[0035] The catalyst is an amine compound and a tin compound, wherein the tin compound is a mixture of 1.0% stannous octoate ...
PUM
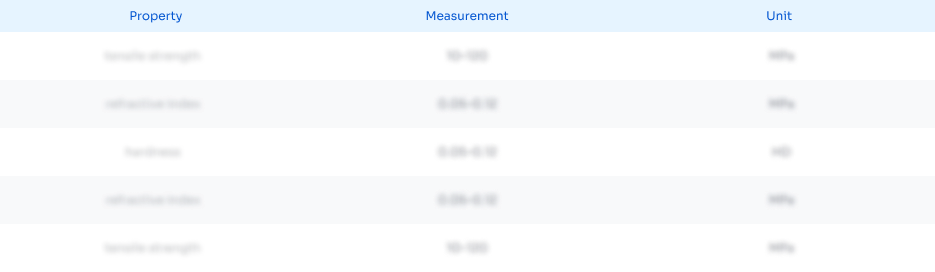
Abstract
Description
Claims
Application Information

- R&D
- Intellectual Property
- Life Sciences
- Materials
- Tech Scout
- Unparalleled Data Quality
- Higher Quality Content
- 60% Fewer Hallucinations
Browse by: Latest US Patents, China's latest patents, Technical Efficacy Thesaurus, Application Domain, Technology Topic, Popular Technical Reports.
© 2025 PatSnap. All rights reserved.Legal|Privacy policy|Modern Slavery Act Transparency Statement|Sitemap|About US| Contact US: help@patsnap.com