Preparation method for isophorone diisocyanate (IPDI) prepolymer for coating curing
A technology of isophorone diisocyanate and prepolymer, which is applied in the field of preparation of isophorone diisocyanate prepolymer for coating curing, can solve the problems of easy yellowing and poor yellowing resistance, and reach the scope of use Wide range, good yellowing resistance, and the effect of lowering the reaction temperature
- Summary
- Abstract
- Description
- Claims
- Application Information
AI Technical Summary
Problems solved by technology
Method used
Image
Examples
Embodiment 1
[0020] Add 100 parts of IPDI, 2 parts of polyether 210 and 0.32 parts of DBTDL into a reaction vessel, raise the temperature to 60°C under the protection of nitrogen, and react for 4 hours to obtain an IPDI prepolymer. Mix 18 parts of TMP with 80 parts of butyl acetate, and dehydrate under reflux at 130° C. for 3 hours through an oil-water separator, and distill 40 parts of butyl acetate. Under the protection of nitrogen, the TMP solution was added dropwise to the IPDI prepolymer, kept at 70° C., and the dropwise addition was completed within 3 hours. Add 0.02 parts of 2,4,6-tris(dimethylaminomethyl)phenol, keep warm at 70°C for 2 hours, measure NCO at 12.15% by toluene-di-n-butylamine method, add 0.05 parts of benzoyl chloride and stir for 30 minutes, cool down Discharge at 40°C, and store under nitrogen gas seal.
[0021] For the compatibility test, 10.17 g of the curing agent prepared in Example 1 and 100 g of the hydroxyacrylic resin were uniformly mixed to obtain a mixed...
Embodiment 2
[0023] Add 100 parts of IPDI, 4 parts of polyether 220 and 0.4 parts of DBTDL into a reaction vessel, raise the temperature to 70°C under the protection of nitrogen, and react for 1.5 hours to obtain an IPDI prepolymer. Mix 16 parts of TMP with 60 parts of butyl acetate, and dehydrate under reflux at 130° C. for 2 hours through an oil-water separator, and distill 20 parts of butyl acetate. Under the protection of nitrogen, the TMP solution was added dropwise to the IPDI prepolymer, kept at 70° C., and the dropwise addition was completed within 3 hours. Add 0.02 parts of 2,4,6-tris(dimethylaminomethyl)phenol, keep warm at 70°C for 2 hours, measure NCO at 12.35% by toluene-di-n-butylamine method, stir 0.05 parts of benzoyl chloride for 30 minutes, cool down to Discharge at 40°C and store in a nitrogen atmosphere.
[0024] For the compatibility test, 10.00 g of the curing agent prepared in Example 2 and 100 g of the hydroxyacrylic resin were uniformly mixed to obtain a mixed liq...
Embodiment 3
[0026] Add 100 parts of IPDI, 4 parts of polyether 303 and 0.2 parts of DBTDL into a reaction vessel, raise the temperature to 60°C under the protection of nitrogen, and react for 3 hours to obtain an IPDI prepolymer. Mix 12 parts of TMP with 60 parts of butyl acetate, and dehydrate under reflux at 130°C for 3 hours through an oil-water separator, and distill 20 parts of butyl acetate. Under the protection of nitrogen, the TMP solution was added dropwise to the IPDI prepolymer, kept at 60° C., and the dropwise addition was completed within 3 hours. Add 0.02 parts of 2,4,6-tris(dimethylaminomethyl)phenol, keep warm at 60°C for 2 hours, measure NCO at 11.50% by toluene-di-n-butylamine method, add 0.1 parts of 85% phosphoric acid and stir for 30 minutes, cool down Discharge at 40°C, and store under nitrogen gas seal.
[0027] For the compatibility test, 10.74 g of the curing agent prepared in Example 3 and 100 g of the hydroxyacrylic resin were uniformly mixed to obtain a mixed ...
PUM
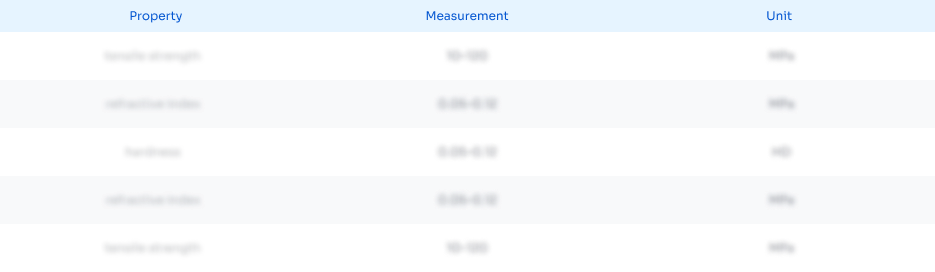
Abstract
Description
Claims
Application Information

- R&D
- Intellectual Property
- Life Sciences
- Materials
- Tech Scout
- Unparalleled Data Quality
- Higher Quality Content
- 60% Fewer Hallucinations
Browse by: Latest US Patents, China's latest patents, Technical Efficacy Thesaurus, Application Domain, Technology Topic, Popular Technical Reports.
© 2025 PatSnap. All rights reserved.Legal|Privacy policy|Modern Slavery Act Transparency Statement|Sitemap|About US| Contact US: help@patsnap.com