Dry-type transformer and reactor casting process
A technology of dry-type transformers and reactors, which is applied in the manufacture of inductors/transformers/magnets, circuits, and electrical components. Economic loss and other issues, to achieve the effect of improving package performance, reducing partial discharge of products, and improving production efficiency
- Summary
- Abstract
- Description
- Claims
- Application Information
AI Technical Summary
Problems solved by technology
Method used
Examples
Embodiment Construction
[0011] First, put the assembled transformers, reactors and other products that need to be poured with epoxy resin into the corresponding casting molds, and fix the transformers, reactors and other products on the bottom plate of the mold with silica gel, and place them at room temperature for 4-10 hours. After the silica gel is cured, put it in an oven to continue curing; the curing time and temperature in the oven vary according to the size, shape and process conditions of the product, the curing time is 2-6 hours, and the curing temperature is 80-100°C. After curing, take the mold out of the oven, cool it to room temperature, pour epoxy resin into the product in the mold according to the design requirements, and then put the mold into a pressurized tank at a temperature of 35-40°C, pressure In the state of 0.5-0.6Mpa, after 2-3 hours until the epoxy resin is completely cured, take out the mold, and then do relevant tests after demoulding, and the products that pass the test a...
PUM
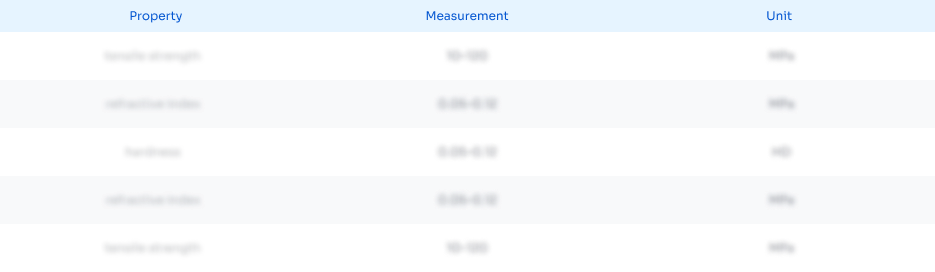
Abstract
Description
Claims
Application Information

- R&D Engineer
- R&D Manager
- IP Professional
- Industry Leading Data Capabilities
- Powerful AI technology
- Patent DNA Extraction
Browse by: Latest US Patents, China's latest patents, Technical Efficacy Thesaurus, Application Domain, Technology Topic, Popular Technical Reports.
© 2024 PatSnap. All rights reserved.Legal|Privacy policy|Modern Slavery Act Transparency Statement|Sitemap|About US| Contact US: help@patsnap.com