High-temperature-resisting aluminum paint used on steel surface, and preparation method thereof
A technology of high temperature resistance and coating, applied in the field of aviation coatings, can solve the problem of only water resistance, and achieve the effects of excellent solvent resistance, salt spray resistance and salt spray resistance.
- Summary
- Abstract
- Description
- Claims
- Application Information
AI Technical Summary
Problems solved by technology
Method used
Image
Examples
preparation example Construction
[0014] As the preparation method of the high-temperature protective aluminum powder coating described above, its component one preparation steps are as follows:
[0015] 1. Dry the pigments and fillers; all the pigments and fillers should be baked in a 110°C drying oven for 2 hours.
[0016] 2. Prepare the resin solution: weigh the resin, additives and solvent according to the ratio of the coating formula, and dissolve it into a uniform mixture;
[0017] 3. Weigh the raw materials; weigh various raw materials according to the proportion of the coating formula;
[0018] 4. Ingredients; put the weighed pigments and fillers into the container to mix, then mix with the resin solution, and stir evenly;
[0019] 5. Grinding: Put the evenly stirred slurry into a sand mill for grinding, and grind for 2 to 3 times in total. During the grinding process, gradually add the remaining solvent to the material to be ground, and form a component after grinding. ,Package.
[0020] When using...
Embodiment 1
[0022] The coating is made by mixing three components in proportion, the weight ratio of component one, component two and component three is 100:3:10; component one is composed of film formers, pigments and fillers, additives and solvents, The weight ratio of its raw materials is film former: pigment and filler: auxiliary agent: solvent is equal to 50:12:3:35; Described film former is made up of modified silicone resin, epoxy resin, amino resin, and its weight Part ratio is modified silicone resin: epoxy resin: amino resin is equal to 34:10:6; described pigment and filler is made up of talcum powder, titanium dioxide, zinc phosphate, fumed silica, and its weight part ratio is talcum powder : titanium dioxide: zinc phosphate: fumed silica is equal to 4: 2: 5: 1; described auxiliary agent is made up of wetting and dispersing agent, aluminum powder orientation agent, and its weight ratio is wetting and dispersing agent: leveling agent : aluminum powder orientation agent is equal ...
Embodiment 2
[0032] The coating is made by mixing three components in proportion, the weight ratio of component one, component two and component three is 100:5:15; component one is composed of film formers, pigments and fillers, additives and solvents, The weight ratio of its raw materials is film former: pigment and filler: auxiliary agent: solvent is equal to 55:12:3:30; Described film former is made of modified silicone resin, epoxy resin, polyester resin, amino resin Composition, its weight ratio is modified silicone resin: epoxy resin: polyester resin: amino resin is equal to 35:8:6:6; Described pigment is made of mica powder, titanium dioxide, aluminum tripolyphosphate, gas Silica composition, its weight ratio is mica powder: titanium dioxide: aluminum tripolyphosphate: fumed silica is equal to 4:2:5:1; described auxiliary agent is made up of wetting and dispersing agent, aluminum powder orientation agent , its weight ratio is wetting and dispersing agent: aluminum powder orientation...
PUM
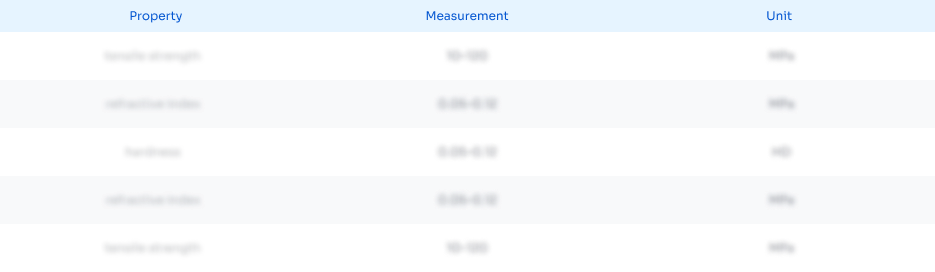
Abstract
Description
Claims
Application Information

- Generate Ideas
- Intellectual Property
- Life Sciences
- Materials
- Tech Scout
- Unparalleled Data Quality
- Higher Quality Content
- 60% Fewer Hallucinations
Browse by: Latest US Patents, China's latest patents, Technical Efficacy Thesaurus, Application Domain, Technology Topic, Popular Technical Reports.
© 2025 PatSnap. All rights reserved.Legal|Privacy policy|Modern Slavery Act Transparency Statement|Sitemap|About US| Contact US: help@patsnap.com