Polyvinylidene fluoride/graphene composite and preparation method thereof
A technology of polyvinylidene fluoride and composite materials, applied in electrical components, capacitors, circuits, etc., can solve problems such as poor dispersion, uneven dispersion, and affecting the performance of composite materials, and achieve simple preparation process, broad application prospects, mechanical good performance
- Summary
- Abstract
- Description
- Claims
- Application Information
AI Technical Summary
Problems solved by technology
Method used
Image
Examples
Embodiment 1
[0035] (1) Disperse 1 g of graphene oxide in 1000 g of deionized water, ultrasonically disperse for 2 h, add 0.5 g of hydroquinone, and react at a temperature of 10 ° C for 48 h. After the reactant is filtered, the filter cake is washed with water for 3 times, Wash with ethanol 3 times to remove excess unreacted hydroquinone, and then vacuum dry to constant weight to obtain graphene.
[0036] (2) Add 0.0005 g of graphene prepared in the first step into 20 mL of DMAc, and ultrasonically disperse for 2 h to obtain a uniform graphene suspension. At the same time, 1 g of PVDF was added to 40 mL of DMAc to prepare a PVDF solution. Then blend the graphene suspension with the PVDF solution, ultrasonically disperse the mixed solution for 2h, then pour the solution into a beaker and place it at 40°C for 36h to allow the DMAc to partially evaporate and thicken, and then dry it in a vacuum oven at 80°C until constant.
[0037] (3) The above-prepared blend was cut into thin slices, and ...
Embodiment 2
[0039] (1) Disperse 3g of graphene oxide in 1000g of deionized water, ultrasonically disperse for 4h, add 5ml of phenylhydrazine, and react at a temperature of 30°C for 24h. After the reactant is filtered, the filter cake is washed with ethanol three times in turn, and washed with DMAc 3 times to remove excess unreacted phenylhydrazine, and then vacuum-dried to constant weight to obtain graphene reduced by phenylhydrazine.
[0040] (2) Add 0.002 g of graphene prepared in the first step into 20 mL of DMAc, and ultrasonically disperse for 3 h to obtain a uniform graphene suspension. At the same time, 1 g of PVDF was added to 40 mL of DMAc to prepare a PVDF solution. Then blend the graphene suspension with the PVDF solution, ultrasonically disperse the mixed solution for 3 h, then pour the solution into a beaker and place it at 50 ° C for 24 h to allow the DMAc to partially evaporate and thicken, and then dry it in a vacuum oven at 80 ° C to constant.
[0041] (3) The above-men...
Embodiment 3
[0043] (1) Disperse 5g of graphene oxide in 1000g of deionized water, ultrasonically disperse for 6h, add 10ml of hydrazine hydrate, and react at a temperature of 60°C for 12h. After the reactant is filtered, the filter cake is washed with water for 3 times and ethanol for 3 times to remove excess unreacted hydrazine hydrate, and then vacuum-dried to constant weight to obtain graphene.
[0044] (2) 0.03 g of graphene prepared in the first step was added to 20 mL of DMAc, and ultrasonically dispersed for 4 hours to obtain a uniform graphene suspension. At the same time, 1 g of PVDF was added to 40 mL of DMAc to prepare a PVDF solution. Then blend the graphene suspension with the PVDF solution, ultrasonically disperse the mixed solution for 4 hours, then pour the solution into a beaker and place it at 70°C for 12 hours to allow the DMAc to partially evaporate and thicken, and then dry it in a vacuum oven at 80°C until constant.
[0045] (3) The blend prepared above was cut int...
PUM
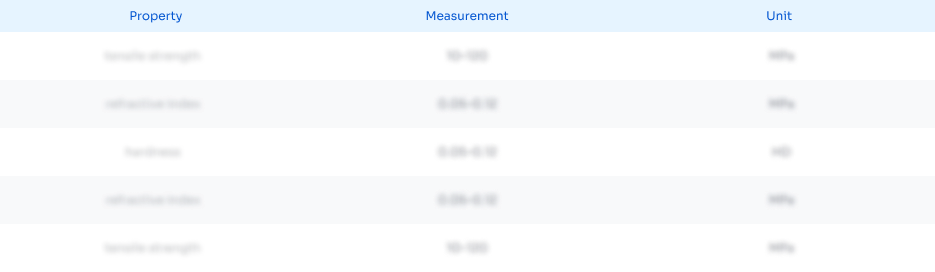
Abstract
Description
Claims
Application Information

- Generate Ideas
- Intellectual Property
- Life Sciences
- Materials
- Tech Scout
- Unparalleled Data Quality
- Higher Quality Content
- 60% Fewer Hallucinations
Browse by: Latest US Patents, China's latest patents, Technical Efficacy Thesaurus, Application Domain, Technology Topic, Popular Technical Reports.
© 2025 PatSnap. All rights reserved.Legal|Privacy policy|Modern Slavery Act Transparency Statement|Sitemap|About US| Contact US: help@patsnap.com