Method for removing fluorine ion from manganese sulfate solution for producing electrolytic manganese metal
A technology of manganese sulfate solution and electrolytic metal manganese, which is applied in the direction of photographic process, instrument, photographic auxiliary process, etc., can solve the problems of inability to produce, reduce current efficiency, corrode anode plate, etc., achieve strong operability and improve utilization rate , the effect of reducing investment
- Summary
- Abstract
- Description
- Claims
- Application Information
AI Technical Summary
Problems solved by technology
Method used
Image
Examples
Embodiment 1
[0021] Add manganese carbonate ore, manganese dioxide ore, pyrite, and sulfuric acid to the leaching tank (7 meters in diameter and 6.5 meters in height) to react and leach manganese sulfate solution, and add calcium carbonate and diatomaceous earth (2:1) as a defluoridation agent For the removal of fluoride ions, see Table 1-1 for the dosage of various raw materials, among which the calcium content in calcium carbonate is ≥50%, the silicon dioxide content in diatomite is ≥90%, and the calcium content is ≤5%.
[0022] After adding the fluoride removal agent, the temperature of the manganese sulfate solution is controlled at 50° C., the pH is controlled at 3.0, and the reaction time is controlled at 50 minutes.
[0023] After the fluorine is removed from the manganese sulfate solution according to the above conditions, the subsequent process is operated according to the original electrolytic manganese metal process to prepare a qualified manganese sulfate solution for the produc...
Embodiment 2
[0034] Add manganese carbonate ore, manganese dioxide ore, pyrite, and sulfuric acid to the leaching tank (7 meters in diameter and 6.5 meters in height) to react and leach manganese sulfate solution, and add calcium carbonate and diatomaceous earth (2:1) as a defluoridation agent For the removal of fluoride ions, see Table 2-1 for the dosage of various raw materials, among which the calcium content in calcium carbonate is ≥50%, the silicon dioxide content in diatomite is ≥90%, and the calcium content is ≤5%.
[0035] After adding the fluoride removal agent, the temperature of the manganese sulfate solution is controlled at 60° C., the pH is controlled at 4.0, and the reaction time is controlled at 40 minutes.
[0036] After the fluorine is removed from the manganese sulfate solution according to the above conditions, the subsequent process is operated according to the original electrolytic manganese metal process to prepare a qualified manganese sulfate solution for the produc...
Embodiment 3
[0048] Add manganese carbonate ore, manganese dioxide ore, pyrite, and sulfuric acid to the leaching tank (7 meters in diameter and 6.5 meters in height) to react and leach manganese sulfate solution, and add calcium carbonate and diatomaceous earth (2:1) as a defluoridation agent For the removal of fluoride ions, see Table 3-1 for the dosage of various raw materials, among which the calcium content in calcium carbonate is ≥50%, the silicon dioxide content in diatomite is ≥90%, and the calcium content is ≤5%.
[0049] After adding the fluoride removal agent, the temperature of the manganese sulfate solution is controlled at 70° C., the pH is controlled at 5.0, and the reaction time is controlled at 35 minutes.
[0050] After removing fluorine from the manganese sulfate solution according to the above conditions, the follow-up process is operated according to the original electrolytic manganese metal process to prepare a qualified manganese sulfate solution for the production of...
PUM
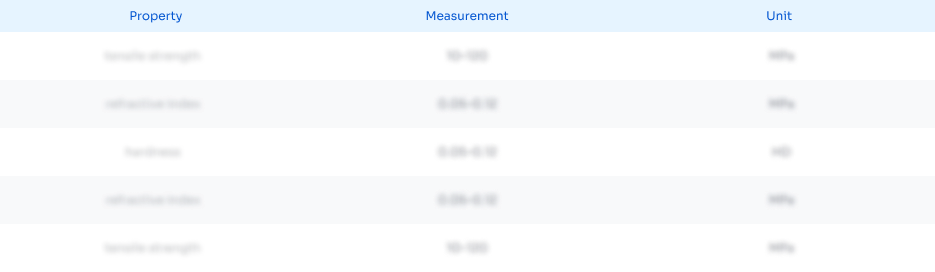
Abstract
Description
Claims
Application Information

- Generate Ideas
- Intellectual Property
- Life Sciences
- Materials
- Tech Scout
- Unparalleled Data Quality
- Higher Quality Content
- 60% Fewer Hallucinations
Browse by: Latest US Patents, China's latest patents, Technical Efficacy Thesaurus, Application Domain, Technology Topic, Popular Technical Reports.
© 2025 PatSnap. All rights reserved.Legal|Privacy policy|Modern Slavery Act Transparency Statement|Sitemap|About US| Contact US: help@patsnap.com