Additive for promoting residual oil thermal cracking reaction and preparing method and application thereof
An additive and thermal cracking technology, which is applied in the chemical industry, can solve the problems of little increase in liquid yield and single function, and achieve the effects of prolonging the start-up period, simple raw materials, and easy access to raw materials
- Summary
- Abstract
- Description
- Claims
- Application Information
AI Technical Summary
Problems solved by technology
Method used
Image
Examples
Embodiment 1
[0023] Pump 38 parts by weight of C9 heavy aromatic solvent oil into the reactor, add 20 parts by weight of thiophosbutane octyl alkyl zinc salt antioxidant preservative, 2 parts by weight of 2,5-dithio-1,3,4- Thiadiazole metal deactivator, 15 parts by weight of polyisobutylene polymaleic anhydride / polyene polyamine-methyl acrylate ashless dispersant, 5 parts by weight of dodecylphenol polyoxyethylene ether emulsifier, warming up to 50 ° C, Stir and dissolve for 15 minutes; then add 15 parts by weight of 2,6-di-tert-butyl-p-cresol antioxidant and 5 parts by weight of hydroquinone polymerization inhibitor into the above solution, keep warm at 55°C, and stir for 35 minutes; cool down to 25°C, discharge and load into barrels.
Embodiment 2
[0025] 38 parts by weight of C10 heavy aromatic hydrocarbon solvent oil are pumped into the reaction kettle, and 20 parts by weight of primary-secondary alkyl zinc salt of sulfur phosphorus, antioxidant preservative, 2 parts by weight of 2,5-dithio-1,3,4-thiazolinol are added successively. Oxadiazole metal deactivator, 15 parts by weight of polyisobutylene succinimide ashless dispersant, 5 parts by weight of octylphenol polyoxyethylene ether emulsifier, heated up to 55 ° C, stirred and dissolved for 12 minutes; then 15 parts by weight of 2 , 6-di-tert-butyl-α-dimethylamino-p-cresol antioxidant and 5 parts by weight of hydroquinone polymerization inhibitor were added to the above solution, kept at 60° C., stirred for 40 minutes; cooled, discharged and loaded into barrels.
Embodiment 3
[0027] 15 parts by weight of C10 heavy aromatic solvent oil are pumped into the reactor, and 25 parts by weight of zinc dialkyldithiophosphate anti-oxidant corrosion inhibitor, 5 parts by weight of trimercapto-s-triazine metal deactivator, 15 parts by weight of poly Isobutylene polymaleic anhydride / polyene polyamine-methyl acrylate ashless dispersant, 10 parts by weight of dodecylphenol polyoxyethylene ether emulsifier, heated to 60 ° C, stirred and dissolved for 10 minutes; then 20 parts by weight of 2, Add 6-di-tert-butyl mixed ester antioxidant and 10 parts by weight of p-benzoquinone polymerization inhibitor to the above solution, keep warm at 50°C, stir for 30 minutes; cool down to 20°C, discharge and load into barrels.
PUM
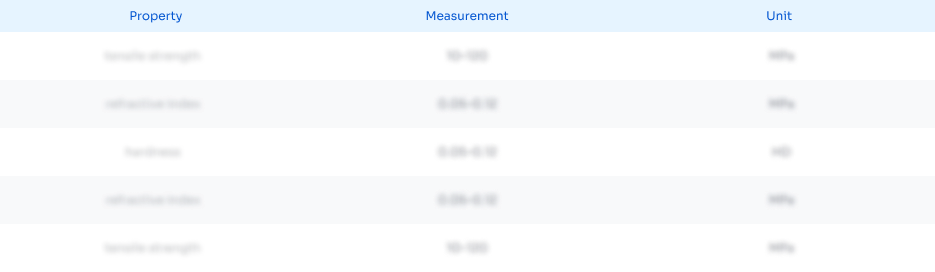
Abstract
Description
Claims
Application Information

- R&D Engineer
- R&D Manager
- IP Professional
- Industry Leading Data Capabilities
- Powerful AI technology
- Patent DNA Extraction
Browse by: Latest US Patents, China's latest patents, Technical Efficacy Thesaurus, Application Domain, Technology Topic, Popular Technical Reports.
© 2024 PatSnap. All rights reserved.Legal|Privacy policy|Modern Slavery Act Transparency Statement|Sitemap|About US| Contact US: help@patsnap.com