High-temperature vacuum carburized gear steel
A carburizing gear, high temperature vacuum technology, applied in the field of alloy steel, can solve problems such as unfavorable steel structure and performance, increase steel production cost, hardenability fluctuation, etc., achieve broad industrial application prospects, reduce CO2 emissions, and improve roughening. effect of temperature
- Summary
- Abstract
- Description
- Claims
- Application Information
AI Technical Summary
Problems solved by technology
Method used
Image
Examples
Embodiment Construction
[0028] The present invention will be further described below in conjunction with embodiment.
[0029] The embodiment is based on the chemical composition range designed by the present invention, smelted on a 50kg vacuum induction furnace, and comparative steels 1 and 2 were smelted by industrial electric furnace + refining outside the furnace + vacuum degassing process. See Table 2 for the specific chemical composition.
[0030] The molten steel of the present invention is cast into an ingot, and is forged to be billeted, and finally forged into a Φ65mm bar, and the final forging temperature is not lower than 1050°C. After the comparison steel is smelted, it is continuously cast into a billet, and continuously rolled into a Φ65mm bar under the condition that the final rolling temperature is not lower than 950°C.
PUM
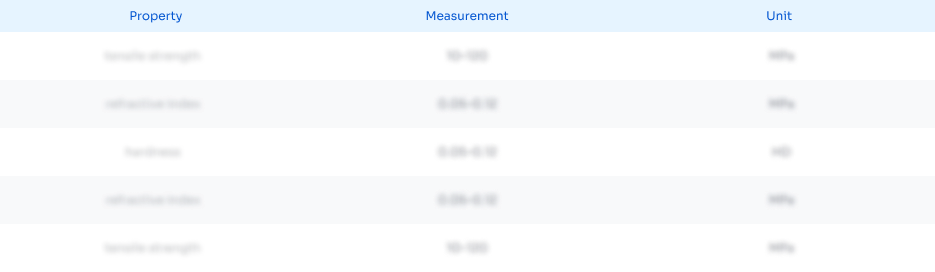
Abstract
Description
Claims
Application Information

- R&D
- Intellectual Property
- Life Sciences
- Materials
- Tech Scout
- Unparalleled Data Quality
- Higher Quality Content
- 60% Fewer Hallucinations
Browse by: Latest US Patents, China's latest patents, Technical Efficacy Thesaurus, Application Domain, Technology Topic, Popular Technical Reports.
© 2025 PatSnap. All rights reserved.Legal|Privacy policy|Modern Slavery Act Transparency Statement|Sitemap|About US| Contact US: help@patsnap.com