Process method for separating glucose from ionic liquid
A technology of ionic liquid and process method, which is applied in the field of anti-solvent separation of glucose and ionic liquid, to achieve the effect of promoting industrialization process, reducing energy consumption, and reducing the use of excessive organic solvents
- Summary
- Abstract
- Description
- Claims
- Application Information
AI Technical Summary
Problems solved by technology
Method used
Examples
Embodiment 1
[0036] This example illustrates the use of acetonitrile as the antisolvent, the mass fraction of glucose in the ionic liquid is 30%, the mass ratio of the ionic liquid to acetonitrile is 1:10, and the precipitation temperature is 30°C to separate glucose from the ionic liquid [BMIM]Cl craft.
[0037] Glucose was dried at 100°C in a forced air drying oven for 24 hours, and the ionic liquid was dried at 50°C under nitrogen for 12 hours. Take a mixed solution of ionic liquid [BMIM]Cl and glucose with a glucose mass fraction of 30%, add it to a 100ml ground-mouth Erlenmeyer flask, place it in an oil bath at 90°C, and stir it magnetically until the mixture forms a transparent solution, then stop heating . After the solution was cooled to room temperature, put it in a water bath at 30°C, add anti-solvent acetonitrile, the mass ratio of [BMIM]Cl to acetonitrile was 1:10, stirred magnetically, and added a small amount of seed crystals. According to the antisolvent principle, glucose...
Embodiment 2
[0040] This example illustrates the use of ethanol as the antisolvent, the mass fraction of glucose in the ionic liquid is 30%, the mass ratio of the ionic liquid to ethanol is 1:5, and the precipitation temperature is 30°C to separate glucose from the ionic liquid [BMIM]Cl craft.
[0041] Glucose was dried at 100°C in a forced air drying oven for 24 hours, and the ionic liquid was dried at 90°C under nitrogen for 12 hours. Take a mixed solution of ionic liquid [BMIM]Cl and glucose with a glucose mass fraction of 30%, add it to a 100ml ground-mouth Erlenmeyer flask, place it in an oil bath at 90°C, and stir it magnetically until the mixture forms a transparent solution, then stop heating . After the solution was cooled to room temperature, put it in a water bath at 30°C, add anti-solvent ethanol, the mass ratio of [BMIM]Cl to ethanol was 1:5, stirred magnetically, and added a small amount of seed crystals. According to the antisolvent principle, glucose begins to precipitate...
Embodiment 3
[0044] This example illustrates the use of ethanol as an antisolvent, the mass fraction of glucose in the ionic liquid is 30%, the mass ratio of ionic liquid to ethanol is 1:15, and the precipitation temperature is 0°C to separate glucose from ionic liquid [BMIM]Cl craft.
[0045] Glucose was dried at 100°C in a forced air drying oven for 24 hours, and the ionic liquid was dried at 90°C under nitrogen for 12 hours. Take a mixed solution of ionic liquid [BMIM]Cl and glucose with a glucose mass fraction of 30%, add it to a 100ml ground-mouth Erlenmeyer flask, place it in an oil bath at 90°C, and stir it magnetically until the mixture forms a transparent solution, then stop heating . After the solution was cooled to room temperature, put it in a salt water bath at 0°C, add anti-solvent ethanol, the mass ratio of [BMIM]Cl to ethanol was 1:15, stirred magnetically, and added a small amount of seed crystals. According to the antisolvent principle, glucose begins to precipitate out...
PUM
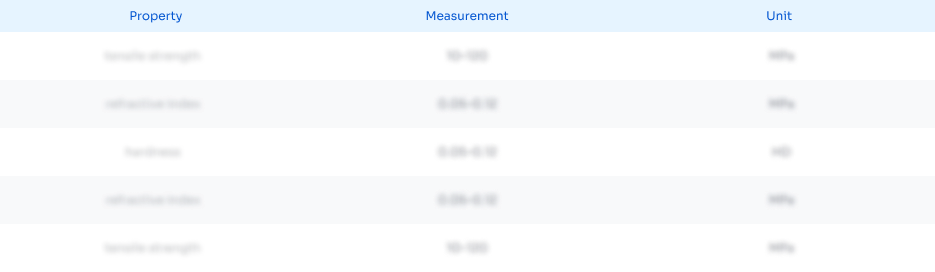
Abstract
Description
Claims
Application Information

- Generate Ideas
- Intellectual Property
- Life Sciences
- Materials
- Tech Scout
- Unparalleled Data Quality
- Higher Quality Content
- 60% Fewer Hallucinations
Browse by: Latest US Patents, China's latest patents, Technical Efficacy Thesaurus, Application Domain, Technology Topic, Popular Technical Reports.
© 2025 PatSnap. All rights reserved.Legal|Privacy policy|Modern Slavery Act Transparency Statement|Sitemap|About US| Contact US: help@patsnap.com