Heat treatment process for bearing steel
A technology of bearing steel and process, which is applied in the field of heat treatment process of GCr15 bearing steel, can solve the problems of high sensitivity to white spots, poor cutting performance and welding performance, general cold working plasticity, etc.
- Summary
- Abstract
- Description
- Claims
- Application Information
AI Technical Summary
Problems solved by technology
Method used
Examples
Embodiment Construction
[0019] The present invention is described in detail below in conjunction with embodiment:
[0020] Carry out heat treatment to GCr15 bearing steel according to the technical scheme provided by the present invention, the chemical composition (weight percentage) of sample is: C 0.90, Mn 0.30, Si 0.25, S 0.020, P 0.025, Cr 1.50.
[0021] The sample was heated to 870°C for austenitization and then quenched. It was kept in a salt bath at 160°C for 20 minutes and then air-cooled. Austenite is thermally stabilized, and after final tempering, the amount of retained austenite increases to 13.2%; the isothermal time is extended to 60min, and the content of retained austenite no longer increases. Immediately after martensite quenching, cold treatment can effectively eliminate residual austenite and reduce it to less than 5%. After the sample martensite isothermal for 60 minutes, a small amount of retained austenite transforms into isothermal martensite, which increases the wear resistan...
PUM
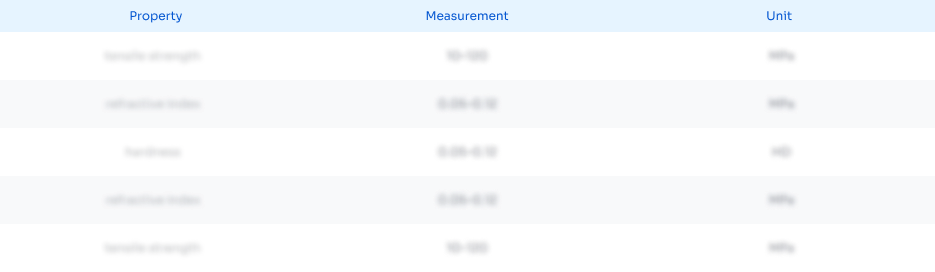
Abstract
Description
Claims
Application Information

- R&D Engineer
- R&D Manager
- IP Professional
- Industry Leading Data Capabilities
- Powerful AI technology
- Patent DNA Extraction
Browse by: Latest US Patents, China's latest patents, Technical Efficacy Thesaurus, Application Domain, Technology Topic, Popular Technical Reports.
© 2024 PatSnap. All rights reserved.Legal|Privacy policy|Modern Slavery Act Transparency Statement|Sitemap|About US| Contact US: help@patsnap.com