Tension device for weaving carbon fibers
A tension device and carbon fiber technology, applied in the direction of fabrics, textiles, looms, etc., can solve the problems of serious hairiness on the surface of carbon fiber bundles, carbon fiber hairiness blocking the warp yarn channel, and affecting the warp yarn density. Fatigue and damage tolerance, effects of improving planar strength
- Summary
- Abstract
- Description
- Claims
- Application Information
AI Technical Summary
Problems solved by technology
Method used
Image
Examples
Embodiment Construction
[0028] This embodiment is a warp tension mechanism for carbon fiber weaving.
[0029] Such as figure 1 shown. The longitudinal tension mechanism of this embodiment includes a support 1, four frame cross braces 2, a pair of wall panels 3, a pair of rear guide rollers 4, four intermediate guide rollers 5, a tension roller 6, and a swing arm 7 , front support 8, leading yarn roller 9.
[0030]The support 1 is the carrier of this embodiment, and is a rectangular frame welded by channel steel. A pair of wall panels 3 are respectively fixed on the upper surface of one end of the two long sides of the support 1, and are fixed with bolts by four frame cross braces 2 to form a support frame. A pair of rear yarn guide rollers 4 are respectively fixed in the mounting grooves of the rear yarn guide rollers 4 at one end of the wallboard; one rear yarn guide roller in the pair of rear yarn guide rollers 4 is located at the other rear yarn guide roller. above the roller, and the lower ci...
PUM
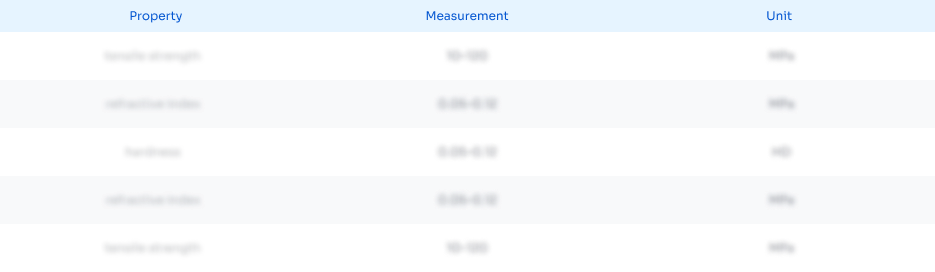
Abstract
Description
Claims
Application Information

- R&D
- Intellectual Property
- Life Sciences
- Materials
- Tech Scout
- Unparalleled Data Quality
- Higher Quality Content
- 60% Fewer Hallucinations
Browse by: Latest US Patents, China's latest patents, Technical Efficacy Thesaurus, Application Domain, Technology Topic, Popular Technical Reports.
© 2025 PatSnap. All rights reserved.Legal|Privacy policy|Modern Slavery Act Transparency Statement|Sitemap|About US| Contact US: help@patsnap.com