Preparation method of microencapsulated gradient halogen-free flame retardant system
A technology of microencapsulation and inorganic flame retardants, which is applied in the field of composite materials, can solve the problems of poor compatibility between halogen-free flame Good combustion effect, low cost, and the effect of improving flame retardancy
- Summary
- Abstract
- Description
- Claims
- Application Information
AI Technical Summary
Problems solved by technology
Method used
Image
Examples
Embodiment 1
[0029] ——Microencapsulation of halogen-free flame retardants:
[0030] a. After uniformly mixing 2.0 grams of ammonium polyphosphate and 1.0 grams of aluminum hydroxide, disperse them in 80 ml of chloroform, then transfer them to a four-necked flask with mechanical stirring and condenser, and heat at a stirring speed of 300 rpm At 55°C, add 30ml of chloroform solution containing 0.1g of toluene diisocyanate dropwise, and then gradually add 0.05g of melamine into the system after the dropwise addition, and continue the reaction for 7 hours, then stop heating and stirring.
[0031] b. Vacuum suction filtration, wash twice with chloroform, then rinse twice with slightly hot distilled water, collect the filter cake, and dry it in a constant temperature vacuum drying oven at 50°C for 12 hours to finally obtain microencapsulated halogen-free barrier Fuel. Calculate the efficiency of microencapsulation.
[0032]
[0033] - Surface modification of pentaerythritol:
[0034] a. Pu...
Embodiment 2
[0040] ——Microencapsulation of halogen-free flame retardants:
[0041] a. After uniformly mixing 1.5 grams of ammonium phosphate and 1.5 grams of aluminum hydroxide, disperse them in 80 ml of chloroform, then transfer them to a four-necked flask with mechanical stirring and condenser, and the stirring speed is 300 rpm and heated to At 55°C, add 40ml of chloroform solution containing 0.1g of toluene diisocyanate dropwise. After the dropwise addition, gradually add 0.06g of melamine into the system and continue the reaction for 7 hours before stopping heating and stirring.
[0042] b. Vacuum suction filtration, wash twice with chloroform, then rinse twice with slightly hot distilled water, collect the filter cake, and dry it in a constant temperature vacuum drying oven at 50°C for 12 hours to finally obtain microencapsulated halogen-free barrier Fuel. Calculate the efficiency of microencapsulation.
[0043]
[0044] - Surface modification of pentaerythritol:
[0045] a. Put ...
Embodiment 3
[0051] ——Microencapsulation of halogen-free flame retardants:
[0052] a. After 1.5 grams of ammonium phosphate and 1.5 grams of magnesium hydroxide are evenly mixed, they are dispersed in 80ml of chloroform, and then transferred to a four-necked flask with mechanical stirring and condenser, and the stirring speed is 300 rpm and heated to At 55°C, add 20ml of chloroform solution containing 0.1g of diphenylmethane diisocyanate dropwise, and then gradually add 0.07g of melamine into the system after the dropwise addition, and continue the reaction for 7 hours, then stop heating and stirring.
[0053] b. Vacuum suction filtration, wash twice with chloroform, then rinse twice with slightly hot distilled water, collect the filter cake, and dry it in a constant temperature vacuum drying oven at 50°C for 12 hours to finally obtain microencapsulated halogen-free barrier Fuel. Calculate the efficiency of microencapsulation.
[0054]
[0055] - Surface modification of pentaerythrit...
PUM
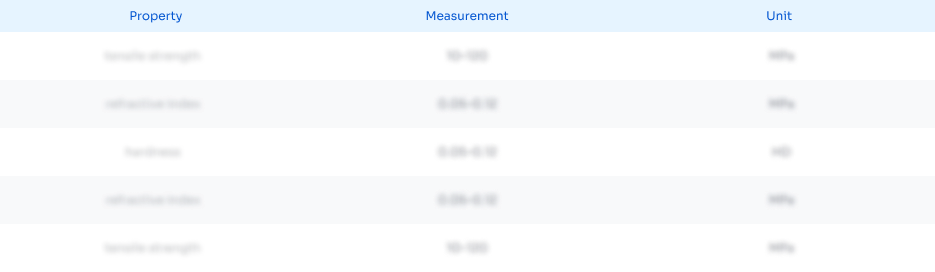
Abstract
Description
Claims
Application Information

- Generate Ideas
- Intellectual Property
- Life Sciences
- Materials
- Tech Scout
- Unparalleled Data Quality
- Higher Quality Content
- 60% Fewer Hallucinations
Browse by: Latest US Patents, China's latest patents, Technical Efficacy Thesaurus, Application Domain, Technology Topic, Popular Technical Reports.
© 2025 PatSnap. All rights reserved.Legal|Privacy policy|Modern Slavery Act Transparency Statement|Sitemap|About US| Contact US: help@patsnap.com