Method for preparing porous material by reversible addition fragmentation chain transfer polymerization of high internal phase emulsion
A technology of high internal phase emulsion and chain transfer polymerization, which is applied in the field of preparation of porous polymer materials by reversible addition-fragmentation chain transfer polymerization of high internal phase emulsion. Improved performance, mechanical properties, good control effects
- Summary
- Abstract
- Description
- Claims
- Application Information
AI Technical Summary
Problems solved by technology
Method used
Image
Examples
Embodiment 1
[0035] Embodiment 1: traditional method prepares porous polymer material
[0036] The oil phase was prepared by mixing 1.934 parts of styrene, 0.822 parts of divinylbenzene, and 0.908 parts of Span 80. An aqueous phase was obtained by mixing 0.252 parts of anhydrous calcium chloride, 0.046 parts of potassium persulfate and 18.251 parts of water. Stir the oil phase at a speed of 400 rpm, add the water phase to the oil phase drop by drop, stir and mix, and continue stirring for 0.5 hours after the addition is complete. Transfer the emulsion into the reactor and raise the temperature to 60°C to initiate polymerization, stop the reaction after 24 hours of polymerization, slowly cool to room temperature and discharge; extract the product and dry it in vacuum to obtain a porous polymer material sample 1, such as figure 1 (a) and (b) shown.
Embodiment 2
[0038] The oil phase was prepared by mixing 1.934 parts of styrene, 0.822 parts of divinylbenzene, 0.070 parts of chain transfer agent RAFT (1), and 0.908 parts of Span80. An aqueous phase was obtained by mixing 0.252 parts of anhydrous calcium chloride, 0.045 parts of potassium persulfate and 18.251 parts of water. Stir the oil phase at a speed of 400 rpm, add the water phase to the oil phase drop by drop, stir and mix, and continue stirring for 0.5 hours after the addition is complete. Put the emulsion into the reactor and raise the temperature to 60°C to initiate polymerization, stop the reaction after 24 hours of polymerization, slowly cool to room temperature and discharge; extract the product and dry it in vacuum to obtain a porous polymer material sample 2, such as figure 1 (c) and (d) shown.
[0039] from figure 1 It can be seen that the wall surface of sample 2 is smoother than that of sample 1, the pinholes in the pore wall disappear, and the number of connecting c...
Embodiment 3
[0044] The oil phase was prepared by mixing 1.934 parts of styrene, 0.822 parts of divinylbenzene, 0.069 parts of chain transfer reagent RAFT (2), and 0.908 parts of Span80. An aqueous phase was obtained by mixing 0.51 parts of anhydrous calcium chloride, 0.09 parts of potassium persulfate and 36.5 parts of water. Stir the oil phase at a speed of 400 rpm, add the water phase to the oil phase drop by drop, stir and mix, and continue stirring for 0.5 hours after the addition is complete. The emulsion was transferred into a reactor and the temperature was raised to 60°C to initiate polymerization. The reaction was stopped after 24 hours of polymerization, and the material was discharged after being slowly cooled to room temperature. The product was extracted and vacuum-dried to obtain a porous polymer material sample 3. Experiments have proved that the wall surface of the porous polymer material prepared in this embodiment is smoother, pinholes are greatly reduced or even disappe...
PUM
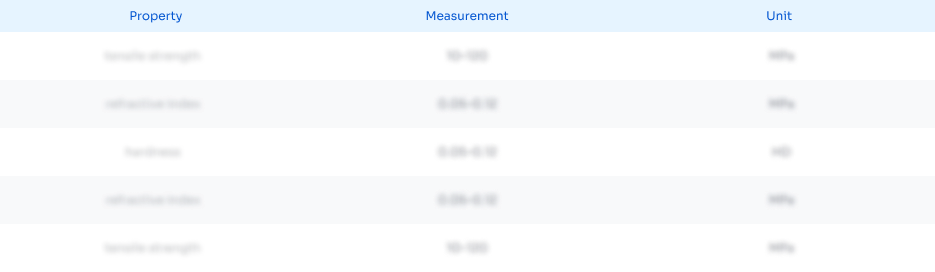
Abstract
Description
Claims
Application Information

- R&D
- Intellectual Property
- Life Sciences
- Materials
- Tech Scout
- Unparalleled Data Quality
- Higher Quality Content
- 60% Fewer Hallucinations
Browse by: Latest US Patents, China's latest patents, Technical Efficacy Thesaurus, Application Domain, Technology Topic, Popular Technical Reports.
© 2025 PatSnap. All rights reserved.Legal|Privacy policy|Modern Slavery Act Transparency Statement|Sitemap|About US| Contact US: help@patsnap.com