Method for forging and cogging magnesium alloy sheet
A technology for magnesium alloys and sheets, which is applied in the field of material forging and rolling, can solve the problems of uneven sheet structure, low pass down pressure, unfavorable rolling deformation, etc., so as to improve and reduce the tendency of slab edge cracking. Processing cost, effect of fine grain structure
- Summary
- Abstract
- Description
- Claims
- Application Information
AI Technical Summary
Problems solved by technology
Method used
Image
Examples
Embodiment 1
[0030] The initial size of the hot-rolled slab is 200×200×70mm, the thickness of which is 70mm, and the side is cross-forged in 3 passes at room temperature (in this example, it can be understood as 20°C), and the strain of each pass is 15%. The sides of the billet are alternately forged along the horizontal and vertical directions, and then heated to 400°C in the furnace for flat roll rolling, which can achieve a single pass of 40% down pressure and basically no cracks on the edge. After 7 passes of flat roll Pressed, the thickness can reach 5mm, and for the sample without side cross forging, the single-pass reduction is only 20%, and the thickness can reach 5mm after 13 rolling passes, and the edge cracks are obvious.
Embodiment 2
[0032] The initial size of the hot-rolled slab is 200×200×70mm, of which the thickness is 70mm. At 150°C, the sides are cross-forged 12 times, and the strain of each pass is 8%. , and then heated to 400°C in a hot furnace for flat roll rolling, which can achieve a single pass of 50% downdraft and basically no cracks on the edge. After 6 passes of rolling, the thickness can reach 6mm without side The single-pass reduction of the cross-forged sample is only 25%, and the thickness can reach 6mm after 12 passes of rolling, and the edge cracks are obvious.
Embodiment 3
[0034] The initial size of the hot-rolled slab is 200×200×70mm, of which the thickness is 70mm. Under the condition of 200°C, the sides are cross-forged 20 times, and the strain of each pass is 2%. Then keep warm in a hot furnace to 300°C and carry out flat roll rolling, which can achieve a single-pass reduction of 40% and basically no cracks on the edge, and can achieve large deformation continuous rolling deformation. After 8 passes of rolling The final thickness can reach 5mm, but for the sample without side cross forging, the single-pass reduction is only 15%, and the thickness can reach 5mm after 15 rolling passes, and the edge cracks are obvious.
[0035] The present invention adopts side cross forging treatment of magnesium alloy slab, so that the material has a large cold deformation at low temperature, and can effectively use the twinned grains to refine the grain size of the as-cast slab, making it After the treatment by the above method, a texture type that is benef...
PUM
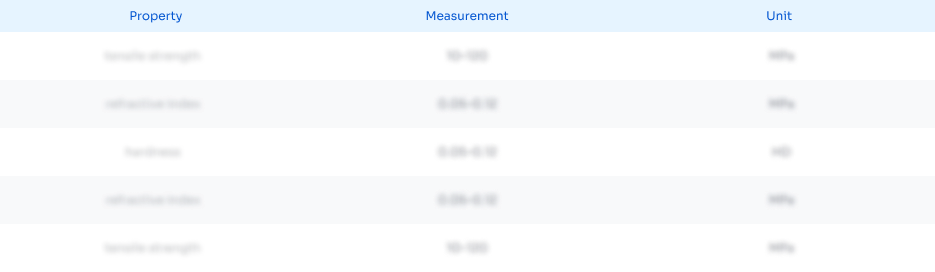
Abstract
Description
Claims
Application Information

- Generate Ideas
- Intellectual Property
- Life Sciences
- Materials
- Tech Scout
- Unparalleled Data Quality
- Higher Quality Content
- 60% Fewer Hallucinations
Browse by: Latest US Patents, China's latest patents, Technical Efficacy Thesaurus, Application Domain, Technology Topic, Popular Technical Reports.
© 2025 PatSnap. All rights reserved.Legal|Privacy policy|Modern Slavery Act Transparency Statement|Sitemap|About US| Contact US: help@patsnap.com