Process method for preparing bricks by using papermaking sludge
A technology of papermaking sludge and process method, applied in clay products, ceramic products, applications, etc., can solve the problems of human and environmental hazards, poisoning, hazards, etc., and achieve the effect of saving clay
- Summary
- Abstract
- Description
- Claims
- Application Information
AI Technical Summary
Problems solved by technology
Method used
Image
Examples
Embodiment 1
[0026] The papermaking sludge brick making process method of the present embodiment comprises steps:
[0027] Step 1: Put the papermaking sludge in the sterilizing treatment tank, add water to the sterilizing treatment tank, and the weight ratio of the amount of water added to the papermaking sludge is 2:1;
[0028] Step 2: Passing disinfection gas into the sterilization treatment pool for sterilization and disinfection treatment;
[0029] Step 3: drying the papermaking sludge after the gas sterilization and disinfection treatment;
[0030] Step 4: Put the dried papermaking sludge, cinder, and clay in a mixing tank for stirring and mixing evenly. The mixing mass ratio of papermaking sludge, cinder, and clay is: 15 parts of papermaking sludge, 12 parts of cinder, and 60 parts of clay ;
[0031] Step 5: Extrude the mixture of cinder, clay and papermaking sludge into billets, cut into bricks, and after drying, sinter the bricks at a sintering temperature of 600-700°C.
Embodiment 2
[0033] The papermaking sludge brick making process method of the present embodiment comprises steps:
[0034] Step 1: Put the papermaking sludge in the sterilizing treatment tank, add water to the sterilizing treatment tank, and the weight ratio of the amount of water added to the papermaking sludge is 2:1;
[0035] Step 2: Passing disinfection gas into the sterilization treatment pool for sterilization and disinfection treatment;
[0036] Step 3: drying the papermaking sludge after the gas sterilization and disinfection treatment;
[0037] Step 4: Put the dried papermaking sludge, cinder, and clay in a mixing tank for stirring and mixing evenly. The mixing mass ratio of papermaking sludge, cinder, and clay is: 25 parts of papermaking sludge, 15 parts of cinder, and 85 parts of clay ;
[0038] Step 5: Extrude the mixture of cinder, clay and papermaking sludge into billets, cut into bricks, and after drying, sinter the bricks at a sintering temperature of 600-700°C.
Embodiment 3
[0040] The papermaking sludge brick making process method of the present embodiment comprises steps:
[0041] Step 1: Put the papermaking sludge in the sterilizing treatment tank, add water to the sterilizing treatment tank, and the weight ratio of the amount of water added to the papermaking sludge is 2:1;
[0042] Step 2: Passing disinfection gas into the sterilization treatment pool for sterilization and disinfection treatment;
[0043] Step 3: drying the papermaking sludge after the gas sterilization and disinfection treatment;
[0044] Step 4: Put the dried papermaking sludge, cinder, and clay in a mixing tank for stirring and mixing evenly. The mixing mass ratio of papermaking sludge, cinder, and clay is: 20 parts of papermaking sludge, 10 parts of cinder, and 70 parts of clay ;
[0045] Step 5: Extrude the mixture of cinder, clay and papermaking sludge into billets, cut into bricks, and after drying, sinter the bricks at a sintering temperature of 600-700°C.
PUM
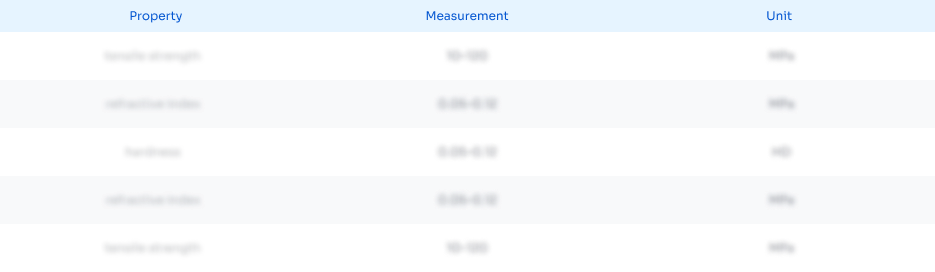
Abstract
Description
Claims
Application Information

- Generate Ideas
- Intellectual Property
- Life Sciences
- Materials
- Tech Scout
- Unparalleled Data Quality
- Higher Quality Content
- 60% Fewer Hallucinations
Browse by: Latest US Patents, China's latest patents, Technical Efficacy Thesaurus, Application Domain, Technology Topic, Popular Technical Reports.
© 2025 PatSnap. All rights reserved.Legal|Privacy policy|Modern Slavery Act Transparency Statement|Sitemap|About US| Contact US: help@patsnap.com