Ferro-titanium alloying method for titaniferous stainless steel
A titanium-iron alloy and stainless steel technology is applied in the field of titanium-iron alloying of titanium-containing stainless steel. rate effect
- Summary
- Abstract
- Description
- Claims
- Application Information
AI Technical Summary
Problems solved by technology
Method used
Examples
Embodiment 1
[0019] The steel type smelted in this embodiment is 321 (0Cr18Ni10Ti), the capacity of the LF refining furnace is 180 tons, and the molten steel is processed 175 tons. There are two bottom blowpipes. The thickness of the slag after the molten steel reaches the LF refining furnace is 50mm. This steel is in the national standard. The mass percentage ratio of the ingredients is:
[0020] C≤0.08; Si≤1.00; Mn≤2.00; Cr 17.00-19.00;
[0021] Ni 9.00-12.00; Ti≥5C; P≤0.035; S≤0.030.
[0022] The applicant controlled the mass percentage ratio of the steel composition to:
[0023] C≤0.04; Si 0.40-0.70; Mn 0.80-1.50; Cr 17.00-18.00;
[0024] Ni 9.00-9.50; Ti 5C-0.25; P≤0.035; S≤0.010.
[0025] The rest is Fe and unavoidable impurities.
[0026] The embodiment of this titanium-containing stainless steel titanium-iron alloying method is the following sequential steps:
[0027] I slag off
[0028] After AOD tapping, remove the slag in the ladle at 01:00:00, and the thickness of the remaining slag is 50mm...
Embodiment 2
[0042] The steel type smelted in this embodiment is 316Ti, the capacity of the LF refining furnace is 180 tons, the molten steel is processed 179 tons, there are two bottom blowpipes, the slag thickness after the molten steel reaches the LF refining furnace is 50mm, and the composition of this steel in the ASTM standard The mass distribution ratio is:
[0043] C≤0.08; Si≤0.75; Mn≤2.00; Cr 16.50-18.50;
[0044] Ni 10.50-13.50; Ti≥5×C+N)-0.70; P≤0.045; S≤0.015.
[0045] The applicant controlled the mass percentage ratio of the steel composition to:
[0046] C≤0.04; Si 0.30-0.70; Mn 0.80-1.50; Cr 16.50-17.00;
[0047] Ni 10.50-11.00; Ti 5×C+N); P≤0.045 S≤0.010 N≤0.020
[0048] The rest is Fe and unavoidable impurities.
[0049] The embodiment of this titanium-containing stainless steel titanium-iron alloying method is the following sequential steps:
[0050] I slag off
[0051] After AOD tapping, remove the slag in the ladle at 03:20:00, and the thickness of the remaining slag is 50mm;
[0052...
Embodiment 3
[0065] The steel type smelted in this embodiment is 409L, the capacity of the LF refining furnace is 180 tons, the molten steel processing is 170.2 tons, there are two bottom blowpipes, the slag thickness after the molten steel reaches the LF refining furnace is 50mm, and the composition of the steel in the JIS standard The mass distribution ratio is:
[0066] C≤0.03; Si≤1.00; Mn≤1.00; Cr 10.50-11.75; Ni≤0.60
[0067] Ti≥6C-0.75; P≤0.035 S≤0.030; N≤0.030.
[0068] The applicant controlled the mass percentage ratio of the steel composition to:
[0069] C≤0.012; Si≤0.75; Mn≤0.80; Cr 11.00-11.75;
[0070] Ni≤0.30; Ti 10×C-0.15; P≤0.035 S≤0.010 N≤0.020
[0071] Nb 0.15-0.20;
[0072] The rest is Fe and unavoidable impurities.
[0073] The embodiment of this titanium-containing stainless steel titanium-iron alloying method is the following sequential steps:
[0074] I slag off
[0075] After AOD tapping, remove the slag in the ladle at 20:20:00, and the thickness of the remaining slag is 50mm;
...
PUM
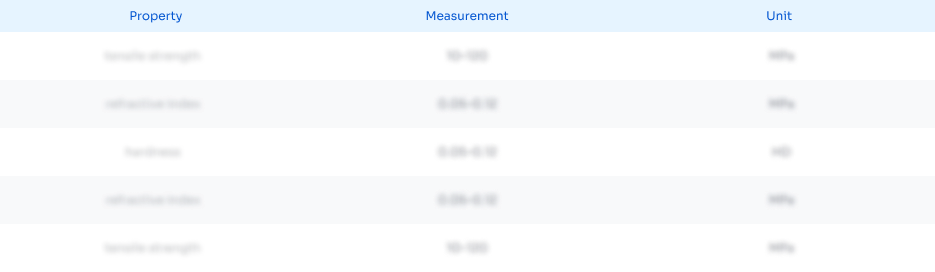
Abstract
Description
Claims
Application Information

- Generate Ideas
- Intellectual Property
- Life Sciences
- Materials
- Tech Scout
- Unparalleled Data Quality
- Higher Quality Content
- 60% Fewer Hallucinations
Browse by: Latest US Patents, China's latest patents, Technical Efficacy Thesaurus, Application Domain, Technology Topic, Popular Technical Reports.
© 2025 PatSnap. All rights reserved.Legal|Privacy policy|Modern Slavery Act Transparency Statement|Sitemap|About US| Contact US: help@patsnap.com