Wafer processing sheet
A technology for thin sheet and wafer processing, which is applied in thin material processing, electrical components, circuits, etc., and can solve problems such as no existing known technology.
- Summary
- Abstract
- Description
- Claims
- Application Information
AI Technical Summary
Problems solved by technology
Method used
Image
Examples
Embodiment 1
[0083] Formation of the anti-adhesion layer
[0084] A monomer mixture of 90 parts by weight of methyl methacrylate (MMA) and 10 parts by weight of hydroxyethyl methacrylate (HEMA) was polymerized to prepare an acrylic polymer having a solid content of 20 wt%. Subsequently, 10 parts by weight of an isocyanate curing agent (TDI) was mixed with the above-mentioned acrylic polymer with respect to 100 parts by weight of the above-prepared acrylic polymer to prepare a coating solution. Then, the above-prepared coating solution was coated on a polyester release film using a bar coater to have a thickness of 2 μm after drying; the coating layer was dried and aged under appropriate conditions to form Anti-blocking layer.
[0085] substrate formation
[0086] A monomer mixture comprising 70 parts by weight of 2-ethylhexyl acrylate (2-EHA), 27 parts by weight of isobornyl acrylate (IBOA) and 3 parts by weight of 2-hydroxyethyl acrylate (2-HEA) was put into the Reflux the 1L conta...
Embodiment 2
[0090]Wafers were processed according to the same method as described in Example 1, except that an isocyanate curing agent (TDI) was not used when forming the anti-blocking layer to form an anti-blocking layer comprising uncured acrylic polymer. to form.
Embodiment 3
[0092] In addition to using cellulose acetate resin instead of a mixture comprising an acrylic polymer and an isocyanate curing agent when forming the anti-blocking layer to form an anti-blocking layer comprising uncured cellulose acetate resin, the sheet for processing the wafer according to the The same method as described in Example 1 was formed.
PUM
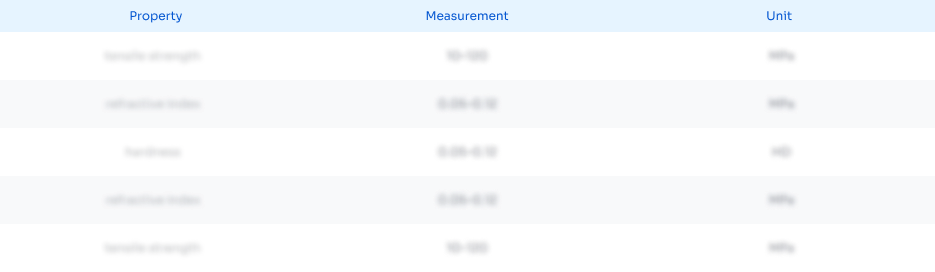
Abstract
Description
Claims
Application Information

- Generate Ideas
- Intellectual Property
- Life Sciences
- Materials
- Tech Scout
- Unparalleled Data Quality
- Higher Quality Content
- 60% Fewer Hallucinations
Browse by: Latest US Patents, China's latest patents, Technical Efficacy Thesaurus, Application Domain, Technology Topic, Popular Technical Reports.
© 2025 PatSnap. All rights reserved.Legal|Privacy policy|Modern Slavery Act Transparency Statement|Sitemap|About US| Contact US: help@patsnap.com