One-time heat treatment method of integral high-speed steel cutter
A heat treatment method and high-speed steel technology, applied in heat treatment furnaces, heat treatment equipment, manufacturing tools, etc., can solve the problems of difficult control of tool quality, reduction of tool red hardness, and difficult work, so as to reduce quenching time, reduce energy consumption, The effect of improving productivity
- Summary
- Abstract
- Description
- Claims
- Application Information
AI Technical Summary
Problems solved by technology
Method used
Image
Examples
Embodiment 1
[0024] Embodiment 1: M2 material countersink heat treatment (such as figure 1 As shown, Ф1=5.5mm, Ф2=12mm, Ф3=8mm, L1=12mm, L2=10mm, L3=60mm)
[0025] (1) Degreasing: Soak the countersink in a chemical degreasing tank at 80°C for 15 minutes, then scrub it with cotton yarn, then wash it with hot water at 90°C, and finally wash it with cold water; the formula of the chemical degreasing tank is: sodium hydroxide 8% , 4% sodium carbonate, 2% sodium silicate, and the balance is water;
[0026] (2) Clamping and drying: Bind the countersink with iron wire, hang the shank upwards and the blade downwards in the drying oven. During the installation and hanging process, try to keep a certain gap between the tools to ensure that the tools are heated evenly. The hanging height is required to be consistent to ensure that the heating position of the knife edge in the salt bath is the same, and then dried at 200°C;
[0027] (3) Preheating: immerse the countersink as a whole in a medium-temp...
Embodiment 2
[0033] Embodiment 2: W18 material countersink heat treatment (such as figure 2 As shown, Ф1=25.3mm, Ф2=12mm, Ф3=22mm, Ф4=24.2mm, Ф5=19.4mm, L1=25mm, L2=98mm, L3=145mm, L4=20mm, H=7.9, α=90o)
[0034] (1) Degreasing: Soak the countersink in a 70°C degreasing tank for 20 minutes, then scrub with cotton yarn, then wash with 80°C hot water, and finally wash with cold water; the chemical degreasing tank formula is: sodium hydroxide 6%, Sodium carbonate 6%, sodium silicate 1%, the balance is water;
[0035] (2) Drying: Bind the countersink drill with iron wire, hang the shank upward and the blade downward in the air resistance heating furnace. During the installation process, try to keep a certain gap between the knives to ensure that the knives are heated evenly. The same hanging height is required to ensure that the heating position of the knife edge in the salt bath is the same, and then dried in a drying oven at 150°C;
[0036] (3) Preheating: immerse the countersink as a who...
Embodiment 3
[0042] Embodiment 3: M2 material end mill heat treatment (such as image 3 with Figure 4 as shown, image 3 Parameters: Ф1=34mm, Ф2=30mm, Ф3=26mm, L1=50mm, L2=108mm, L3=338mm; Figure 4 Parameter: L=32mm)
[0043] (1) Degreasing: Soak the end mill in a chemical degreasing tank at 90°C for 30 minutes, then scrub it with cotton yarn, then wash it with hot water at 100°C, and finally wash it with cold water; the formula of the chemical degreasing tank is: sodium hydroxide 10 %, sodium carbonate 3%, sodium silicate 3%, the balance is water;
[0044] (2) Drying: Use M14 bolts to pass through the hanging plate, and screw the other end into it Figure 4 The handle of the end mill is then dried in a drying oven at 250°C. During drying, the hanging height is required to be consistent to ensure that the heating position of the cutting edge in the salt bath is the same;
[0045](3) Preheating: immerse the end mill as a whole in a medium-temperature salt bath at 840°C, and keep it w...
PUM
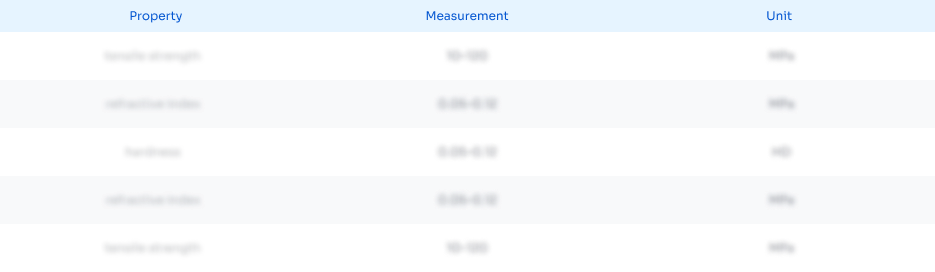
Abstract
Description
Claims
Application Information

- R&D Engineer
- R&D Manager
- IP Professional
- Industry Leading Data Capabilities
- Powerful AI technology
- Patent DNA Extraction
Browse by: Latest US Patents, China's latest patents, Technical Efficacy Thesaurus, Application Domain, Technology Topic, Popular Technical Reports.
© 2024 PatSnap. All rights reserved.Legal|Privacy policy|Modern Slavery Act Transparency Statement|Sitemap|About US| Contact US: help@patsnap.com