Power module and method for manufacturing same
A technology of a power module and a manufacturing method, which is applied in the manufacturing of semiconductor/solid-state devices, electrical components, and electric solid-state devices, etc., can solve the problems of reduced joint reliability, reduced joint reliability, and increased operating temperature, and can prevent reliability. Deterioration, thermal stress suppression, and quality improvement effects
- Summary
- Abstract
- Description
- Claims
- Application Information
AI Technical Summary
Problems solved by technology
Method used
Image
Examples
Embodiment approach 1
[0024]
[0025] The power module according to Embodiment 1 of the present invention will be described using the drawings. Such as figure 1 As shown, the power module of the present invention is provided in the box body 8 with: a bottom plate 7; an insulating substrate 5 is arranged on the bottom plate 7 through the solder 6; a power element 1 is arranged on the insulating substrate 5 through the solder 6; The wiring member 9 as the first wiring member is bonded to the surface electrode of the power element 1 via the bonding material 10; the terminal 4 is connected to the wiring member 9 via the aluminum wire 3 as wiring; and the sealing material 2 is filled in the case 8 And covers insulating substrate 5 , power element 1 , wiring member 9 , and aluminum wire 3 . By using SiC or the like, which is a wideband gap semiconductor, as the power element 1 , a device capable of operating at a higher temperature can be realized.
[0026] The wiring member 9 is made of a highly con...
Embodiment approach 2
[0038]
[0039] Figure 4 A power module according to Embodiment 2 is shown. As shown in the figure, in addition to the configuration of the power module shown in Embodiment 1, the power module further includes a wiring member 91 having a first side surface bonded to the insulating substrate 5 as a second wiring member. The rectangular cylindrical metal on the surface pattern connects the wiring member 91 and the terminal 4 via the aluminum wire 3 .
[0040] Here, the sealing material 2 can also be filled in the case body 8 as in the first embodiment, but in the second embodiment, the aluminum wire 3 is used on the side surface (the second side surface) where the wiring member 9 and the wiring member 91 are joined. ) is filled with a sealing material 100 (first sealing material) such as epoxy resin and cured so that at least it is exposed, and then the aluminum wire 3 is bonded to the exposed surfaces of the wiring members 9 and 91 . After that, the remaining exposed porti...
Embodiment approach 3
[0049]
[0050] Figure 5 A power module in the case of using a plurality of power elements connected in parallel in Embodiment 3 is shown. As shown in the figure, in addition to the configuration of the power module shown in Embodiment 2, the power module of Embodiment 3 further includes a wiring member 90, and the wiring members provided corresponding to each power element 1 are arranged on the second side surface side. joined to each other.
[0051] The wiring member 90 is an integral structure straddling a plurality of power elements 1 . With this structure, the intensity of ultrasonic vibrations to withstand the weight applied at the time of joining the aluminum wire 3 is further increased compared to Embodiment 2, and the surface area for heat dissipation is also increased due to the formation of the connection portion. Therefore, a further heat dissipation effect can be expected.
[0052]
[0053] According to Embodiment 3 of the present invention, in the power m...
PUM
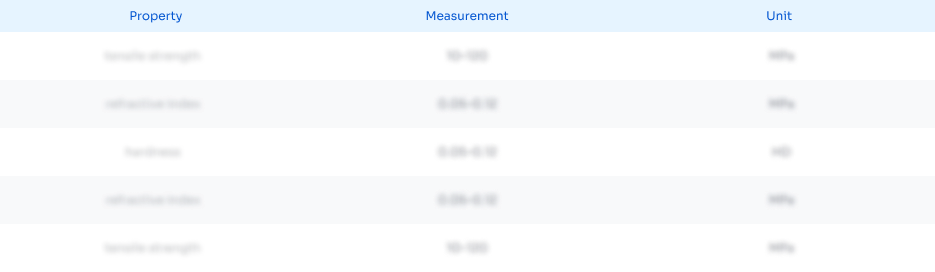
Abstract
Description
Claims
Application Information

- R&D
- Intellectual Property
- Life Sciences
- Materials
- Tech Scout
- Unparalleled Data Quality
- Higher Quality Content
- 60% Fewer Hallucinations
Browse by: Latest US Patents, China's latest patents, Technical Efficacy Thesaurus, Application Domain, Technology Topic, Popular Technical Reports.
© 2025 PatSnap. All rights reserved.Legal|Privacy policy|Modern Slavery Act Transparency Statement|Sitemap|About US| Contact US: help@patsnap.com