Coal power plant combined type heat pipe flue gas waste heat recovery system and method
A flue gas waste heat recovery system technology, applied in combustion methods, preheating, feed water heaters, etc., can solve problems such as increasing layout space, fouling of equipment, affecting heat exchange efficiency, etc., reducing workload and easy disassembly. The effect of replacing and saving water resources
- Summary
- Abstract
- Description
- Claims
- Application Information
AI Technical Summary
Problems solved by technology
Method used
Image
Examples
Embodiment Construction
[0068]The preferred embodiments of the present invention will be described below in conjunction with the accompanying drawings. It should be understood that the preferred embodiments described here are only used to illustrate and explain the present invention, and are not intended to limit the present invention.
[0069] System embodiment
[0070] According to an embodiment of the present invention, such as Figure 2a-Figure 5c As shown, a coal power plant combined heat pipe flue gas waste heat recovery system is provided.
[0071] Such as image 3 As shown, this embodiment includes a boiler 4 , a dust collector 5 , an induced draft fan 6 , a booster fan 8 , a combined heat pipe heat exchanger assembly, a desulfurization tower 26 and a chimney 1 that are sequentially connected through pipelines.
[0072] Here, in the combined heat pipe heat exchanger assembly, the heat pipe is a high-efficiency heat exchange element that is filled with a working medium in the closed tube s...
PUM
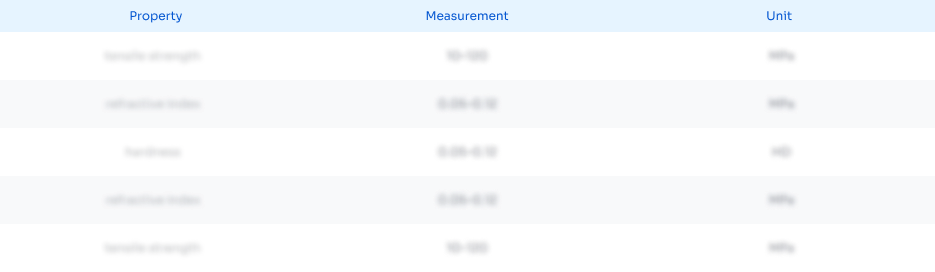
Abstract
Description
Claims
Application Information

- R&D
- Intellectual Property
- Life Sciences
- Materials
- Tech Scout
- Unparalleled Data Quality
- Higher Quality Content
- 60% Fewer Hallucinations
Browse by: Latest US Patents, China's latest patents, Technical Efficacy Thesaurus, Application Domain, Technology Topic, Popular Technical Reports.
© 2025 PatSnap. All rights reserved.Legal|Privacy policy|Modern Slavery Act Transparency Statement|Sitemap|About US| Contact US: help@patsnap.com