Method for removing polished section crystal round edge used for IGBT (insulated gate bipolar transistor) in a row grinding manner
A polishing wafer and oxide film technology, applied in the field of back treatment, can solve the problems of reducing the effective area of epitaxy, operator injury, high cost and high cost, and achieve the effect of being conducive to mass production, improving production efficiency and high production efficiency
- Summary
- Abstract
- Description
- Claims
- Application Information
AI Technical Summary
Problems solved by technology
Method used
Image
Examples
Embodiment 1
[0042] The traditional method of pasting the special blue film by hand in the present invention is changed to use a scratch-type semi-automatic edge removal machine to prepare circular plastic blue films of different specifications, thereby completing the removal of the oxide film on the back of the wafer. Concrete preparation process is as follows:
[0043] 1) Prepare a 6-inch (diameter 150mm) single-crystal silicon wafer with a thickness of 642 μm, As dopant, crystal orientation, and a resistivity of 0.002-0.004 after back damage and back sealing; prepare a plastic blue film As an auxiliary material, the material is PVC, the thickness is 380μm, the width is 160mm, and the length of a roll is 10m;
[0044] 2) Take it out of the blue film, with the back cover facing down and the front facing up, and stick them on the roll plastic blue film in turn,
[0045] 3) After the heat shrinking machine is preheated, pass the rolled plastic blue film adhered to the silicon wafer th...
PUM
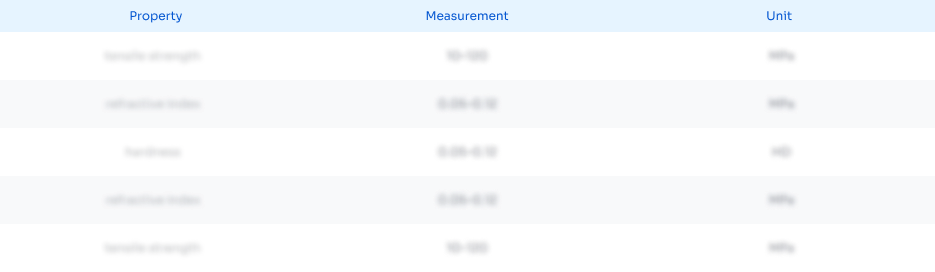
Abstract
Description
Claims
Application Information

- R&D Engineer
- R&D Manager
- IP Professional
- Industry Leading Data Capabilities
- Powerful AI technology
- Patent DNA Extraction
Browse by: Latest US Patents, China's latest patents, Technical Efficacy Thesaurus, Application Domain, Technology Topic, Popular Technical Reports.
© 2024 PatSnap. All rights reserved.Legal|Privacy policy|Modern Slavery Act Transparency Statement|Sitemap|About US| Contact US: help@patsnap.com