Combined type heat-insulating baffle for increasing monocrystal solidification temperature gradient
A heat insulation baffle and solidification temperature technology, which is applied in the directions of single crystal growth, self-solidification method, crystal growth, etc., can solve the problems of production process interruption, affecting heat insulation effect, time-consuming molybdenum sheet processing, etc., and achieves low price and cost, The effect of low cost and simple processing
- Summary
- Abstract
- Description
- Claims
- Application Information
AI Technical Summary
Problems solved by technology
Method used
Image
Examples
Embodiment 1
[0016] In the ZGD-1 vacuum induction directional solidification furnace, a composite heat insulation baffle is used. The inner and outer diameters of the annular body of the composite heat insulation baffle are Φ200mm and Φ250mm, the total height of the annular body is 150mm, and the outer diameter of the upper graphite ring is is 100mm, and the inner diameter of the upper graphite ring is 50mm. After testing, the temperature gradient increased from the usual 40-60°C / cm to 60-80°C / cm.
Embodiment 2
[0018] In the DSP II vacuum induction directional solidification furnace, a composite heat insulation baffle is used. The inner and outer diameters of the annular body of the composite heat insulation baffle are Φ220mm and Φ270mm, the total height of the annular body is 150mm, and the outer diameter of the upper graphite ring is is 100mm, and the inner diameter of the upper graphite ring is 50mm. After testing, the temperature gradient changed from the usual 30-60°C / cm to 50-70°C / cm.
PUM
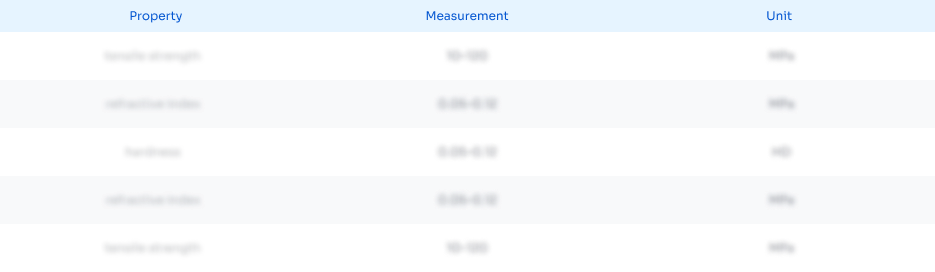
Abstract
Description
Claims
Application Information

- Generate Ideas
- Intellectual Property
- Life Sciences
- Materials
- Tech Scout
- Unparalleled Data Quality
- Higher Quality Content
- 60% Fewer Hallucinations
Browse by: Latest US Patents, China's latest patents, Technical Efficacy Thesaurus, Application Domain, Technology Topic, Popular Technical Reports.
© 2025 PatSnap. All rights reserved.Legal|Privacy policy|Modern Slavery Act Transparency Statement|Sitemap|About US| Contact US: help@patsnap.com