Roasting pretreatment process for extracting vanadium pentoxide from high-carbon scherbinaite-containing coal mine and vanadium pentoxide extracting method
A vanadium pentoxide and oxidative roasting technology, applied in the direction of improving process efficiency, etc., can solve problems such as difficult thermal control, difficulty in stable combustion, and pollution of three wastes, achieve good prospects for popularization and application, and reduce heat consumption and energy consumption , the effect of reducing operating costs
- Summary
- Abstract
- Description
- Claims
- Application Information
AI Technical Summary
Problems solved by technology
Method used
Examples
Embodiment 1
[0028] A high-carbon stone coal vanadium deposit in a certain place in Northwest China, the chemical composition of the raw ore mainly includes C 20.25%, SiO2 55.67%, Al 2 o 3 9.92%, V 2 o 5 0.757%, P 1.35% and Fe 7.56%, adopt the technology of the present invention to process this high-carbon stone coal vanadium ore, specifically comprise the following steps:
[0029] 1. Roasting pretreatment
[0030] The high-carbon stone coal-vanadium ore in this example is first crushed (various operations including jaw crushing, double-roller, ball milling, crushing, etc.) can be used to -100 mesh, accounting for about 80%, and then an appropriate amount (moisture content The water with content up to 8%) is highly mixed by the mixer (wheel mill), and then the water is mixed by the press at 120kgf / cm 2 Continuous briquetting under pressure, the pressed stone coal blocks are mechanically stacked into a brick stack of a certain height according to the appropriate spacing, and are cont...
Embodiment 2
[0034] A high-carbon stone coal vanadium mine in Hunan, the chemical composition of the raw ore includes C 12.65%, SiO 2 71.28%, Al 2 o 3 7.35%, V 2 o 5 0.92%, P 0.35% and Fe 1.39%, adopt technology of the present invention to process this high-carbon stone coal vanadium ore, specifically comprise the following steps:
[0035] 1. Roasting pretreatment
[0036] The high-carbon stone coal vanadium ore in this example is crushed first (various operations including jaw crushing, double rollers, ball milling, crushing, etc. can be used) to -100 mesh, accounting for about 80%, and then an appropriate amount of water is added to The mixing machine (wheel mill) is highly mixed until the moisture content reaches 10%, and then the pressure is 160kgf / cm by the press 2 Continuous briquetting under pressure, the pressed stone coal blocks are mechanically stacked into a brick stack of a certain height according to the appropriate spacing, and are continuously put into the drying kil...
PUM
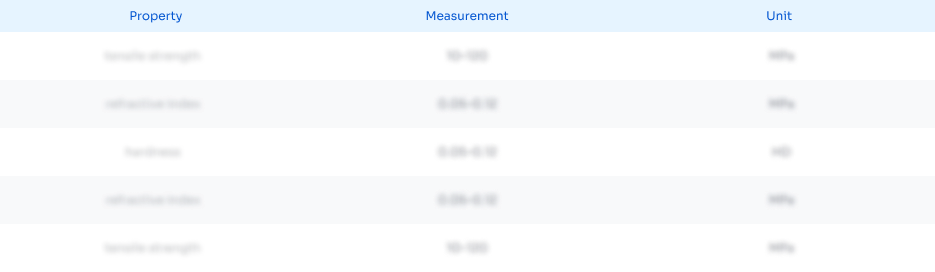
Abstract
Description
Claims
Application Information

- R&D
- Intellectual Property
- Life Sciences
- Materials
- Tech Scout
- Unparalleled Data Quality
- Higher Quality Content
- 60% Fewer Hallucinations
Browse by: Latest US Patents, China's latest patents, Technical Efficacy Thesaurus, Application Domain, Technology Topic, Popular Technical Reports.
© 2025 PatSnap. All rights reserved.Legal|Privacy policy|Modern Slavery Act Transparency Statement|Sitemap|About US| Contact US: help@patsnap.com