Cooling system for die and casting process
A cooling system and mold technology, applied in the field of casting engineering, can solve the problems of long casting process duration, high energy consumption, slow cooling speed, etc., and achieve the effect of reducing process duration, energy consumption and noise, and improving water cooling efficiency
- Summary
- Abstract
- Description
- Claims
- Application Information
AI Technical Summary
Problems solved by technology
Method used
Image
Examples
Embodiment Construction
[0018] Next, the specific implementation of a cooling system for a mold and a casting process according to the present invention will be described in detail with reference to the accompanying drawings.
[0019] Attached figure 1 Shown is a schematic structural diagram of the cooling system for a mold according to this embodiment, which includes a mold body 10 and a cooling device. The cooling device is water-cooled and includes a plurality of cooling units closely attached to the surface of the mold body 10. In this embodiment, the mold body 10 is a mold for automobile wheels. According to the structural characteristics of the mold, the cooling unit includes PCD water cooling 21, lower mold slope water cooling 22, rib water cooling 23, rib tail water cooling 24, split core water cooling 25, and Surface water cooling 26, upper mold slope water cooling 27 and side mold rib tip water cooling 28.
[0020] PCD water cooling 21 and lower mold slope water cooling 22 each use independent i...
PUM
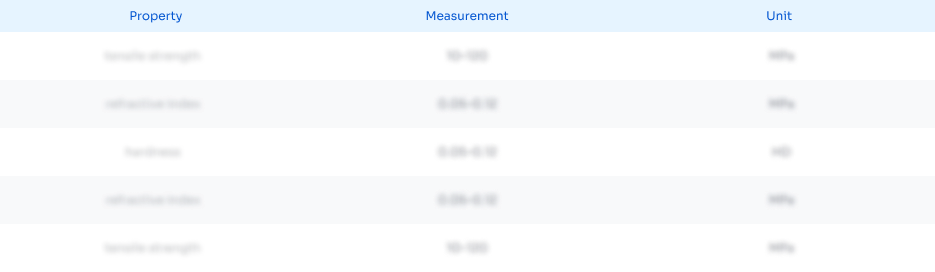
Abstract
Description
Claims
Application Information

- R&D Engineer
- R&D Manager
- IP Professional
- Industry Leading Data Capabilities
- Powerful AI technology
- Patent DNA Extraction
Browse by: Latest US Patents, China's latest patents, Technical Efficacy Thesaurus, Application Domain, Technology Topic, Popular Technical Reports.
© 2024 PatSnap. All rights reserved.Legal|Privacy policy|Modern Slavery Act Transparency Statement|Sitemap|About US| Contact US: help@patsnap.com