Production technology of preparing manganeisen from low grade manganese mine
A low-grade manganese ore and production process technology are applied in the field of low-grade manganese ore to prepare ferromanganese alloy production technology, and can solve the problems of complex manganese manufacturing process, huge environmental load, serious environmental pollution and the like
- Summary
- Abstract
- Description
- Claims
- Application Information
AI Technical Summary
Problems solved by technology
Method used
Examples
Embodiment 1
[0018] Dry the low-grade manganese ore with a metal manganese content of 16%, grind it into a 200-mesh powder, assume that the manganese ore is MnO, and add a reducing agent that is 1.5 times the theoretically calculated mass required to reduce MnO to metal. The reducing agent is metal aluminum and coke, of which aluminum accounts for 30% of the total reducing agent, and coke accounts for 70% of the total reducing agent; catalyst manganese oxide, iron powder and vanadium pentoxide are added at 1.5% of the total mass of low-grade manganese ore , wherein manganese oxide accounts for 30% of the total mass of the catalyst, iron powder accounts for 40% of the total mass of the catalyst, and vanadium pentoxide accounts for 30% of the total mass of the catalyst; add solvent according to 1.0% of the total mass of low-grade manganese ore, and the solvent composition is oxidation Potassium accounts for 60% of the total mass of the solvent, fluorite accounts for 40% of the total mass of t...
Embodiment 2
[0022] The low-grade manganese ore with a metal manganese content of 29% is dried and ground into a 100-mesh powder. Assuming that the manganese ore is MnO, the reducing agent is used to reduce MnO to 1.1 times the theoretically calculated mass required to reduce MnO to metal. The reducing agent is metal aluminum, silicon carbide and graphite-like, of which aluminum accounts for 15% of the total mass of the reducing agent, coke accounts for 45% of the total mass of the reducing agent, silicon carbide accounts for 30% of the total mass of the reducing agent, and graphite-like 10% of the total mass; add catalyst manganese oxide, iron powder and vanadium pentoxide by 0.25% of the total mass of low-grade manganese ore, wherein manganese oxide accounts for 45% of the total mass of the catalyst, and iron powder accounts for 40% of the total mass of the catalyst. Vanadium pentoxide accounts for 15% of the total mass of the catalyst; 0.30% of the total mass of low-grade manganese ore i...
Embodiment 3
[0026]Dry the low-grade manganese ore with a metal manganese content of 21%, and grind it into a 150-mesh powder. Assuming that the manganese ore is MnO, and using a reducing agent to reduce MnO to metal, 1.25 times the theoretically calculated mass is added to add a reducing agent. The reducing agent is metal aluminum, calcium carbide and coke, wherein aluminum accounts for 20% of the total mass of the reducing agent, coke accounts for 45% of the total mass of the reducing agent, and calcium carbide accounts for 35% of the total mass of the reducing agent. 0.8% add catalyst manganese oxide, iron powder and vanadium pentoxide, wherein manganese oxide accounts for 30% of the total mass of the catalyst, iron powder accounts for 45% of the total amount of the catalyst, and vanadium pentoxide accounts for 25% of the total amount of the catalyst; 0.6% of the total mass of manganese ore is added as a solvent, and the solvent is composed of potassium oxide accounting for 50% of the to...
PUM
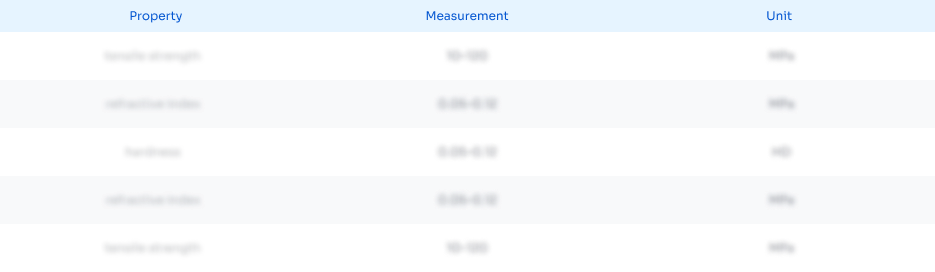
Abstract
Description
Claims
Application Information

- R&D
- Intellectual Property
- Life Sciences
- Materials
- Tech Scout
- Unparalleled Data Quality
- Higher Quality Content
- 60% Fewer Hallucinations
Browse by: Latest US Patents, China's latest patents, Technical Efficacy Thesaurus, Application Domain, Technology Topic, Popular Technical Reports.
© 2025 PatSnap. All rights reserved.Legal|Privacy policy|Modern Slavery Act Transparency Statement|Sitemap|About US| Contact US: help@patsnap.com