Packaging method for light-emitting manner of LED (Light-Emitting Diode) with specific wavelength
A technology with a specific wavelength and packaging method, which is applied in the direction of electrical components, circuits, semiconductor devices, etc., can solve the problems of high R&D cost, long cycle, poor color rendering, etc., and achieves easier control of stability, short production cycle, and color rendering good sex effect
- Summary
- Abstract
- Description
- Claims
- Application Information
AI Technical Summary
Problems solved by technology
Method used
Image
Examples
Embodiment 1
[0027] See figure 1 , The raw materials of this embodiment include raw materials A glue, B glue, DP glue, yellow phosphor with color coordinates of x=0.462, Y=0.527, LED blue chip with wavelength of 455nm, color coordinates of x=10.95, y= 32.33 yellow pigment. Among them, A glue refers to epoxy resin photoelectric castable WL-700A-8, which includes bisphenol A epoxy resin, epoxy diluent and additives; B glue refers to epoxy resin photoelectric castable WL-700B-8, It includes acid anhydride curing agent and accelerator; DP glue refers to epoxy resin light diffusing agent DF-090, which includes bisphenol A epoxy resin and light diffusing agent; A glue, B glue and DP glue are mixed mainly for packaging , Curing. In this embodiment, the tools for packaging the LED are the LED bracket 1, the bowl cavity 2 and the oven, and the specific preparation method is as follows:
[0028] (1) Preheat glue A and glue DP in an oven, the temperature of the oven is 60±5℃, and the preheating time ...
Embodiment 2
[0039] This embodiment is to make a pink LED with a specific wavelength. The process method is basically the same as that of embodiment 1, the main difference is:
[0040] In step (6), the yellow pigment with color coordinates x=10.95 and y=32.33 is replaced with red pigment with color coordinates x=0.16 and Y=0.62. The weight parts of each component are: A glue 1000 parts, B 950 parts of glue, color coordinates of x=0.16, Y=0.62, 20 parts of red pigment, the components are evenly mixed to form epoxy glue.
[0041] The other steps are the same as in Example 1, and finally an LED with a specific wavelength color coordinate of x=0.38 and Y=0.16 is produced, and the light-emitting source is pink.
PUM
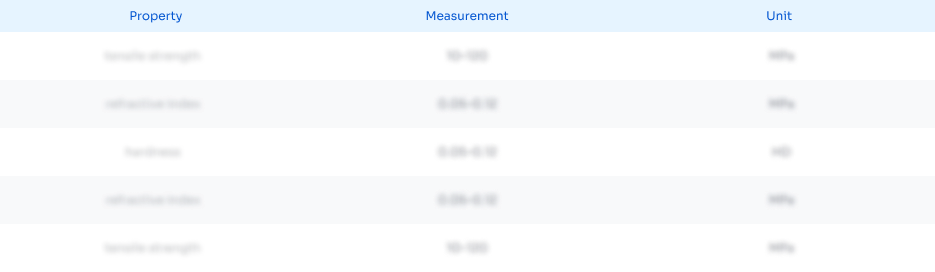
Abstract
Description
Claims
Application Information

- R&D
- Intellectual Property
- Life Sciences
- Materials
- Tech Scout
- Unparalleled Data Quality
- Higher Quality Content
- 60% Fewer Hallucinations
Browse by: Latest US Patents, China's latest patents, Technical Efficacy Thesaurus, Application Domain, Technology Topic, Popular Technical Reports.
© 2025 PatSnap. All rights reserved.Legal|Privacy policy|Modern Slavery Act Transparency Statement|Sitemap|About US| Contact US: help@patsnap.com