Preparation method of high-residual internal stress Ni-Mn-Ga magnetically-driven memory alloy film
A technology of ni-mn-ga and memory alloy, applied in metal material coating process, ion implantation plating, coating, etc., can solve the problem of high magnetic field threshold, achieve high residual compressive stress and reduce magnetic field threshold Effect
- Summary
- Abstract
- Description
- Claims
- Application Information
AI Technical Summary
Problems solved by technology
Method used
Image
Examples
Embodiment 1
[0021] The preparation method of this large residual internal stress Ni-Mn-Ga magnetic drive memory alloy film is as follows,
[0022] 1. To prepare the Ni-Mn-Ga alloy target material, three metals with a purity of 99.99wt%-Ni, 99.9wt%-Mn and 99.99wt%-Ga were respectively taken as 47 parts, 32 parts and 21 parts according to the molar ratio Proportioning raw materials, using a non-consumable vacuum electric arc furnace to prepare targets under an argon protective atmosphere, its chemical composition is Ni47Mn32Ga21 (at%); before smelting, use a mechanical pump and a molecular pump to evacuate the electric arc furnace to 1×10 -3 Pa, and then filled with high-purity argon with a volume concentration of 99.999% to control the vacuum at 2×10 -2 About Pa; after starting smelting, turn over the smelting four times and add magnetic stirring, take it out after cooling; use wire cutting method to cut it into a circular target with a size of ?60mm×2mm, and remove surface impurities by m...
Embodiment 2
[0026] The difference between the preparation method of the large residual internal stress Ni-Mn-Ga magnetically driven memory alloy thin film in this embodiment and the embodiment 1 is that the substrate bias voltage is 10V.
Embodiment 3
[0028] The difference between the preparation method of the large residual internal stress Ni-Mn-Ga magnetically driven memory alloy thin film in this embodiment and the embodiment 1 is that the substrate bias is 20V.
PUM
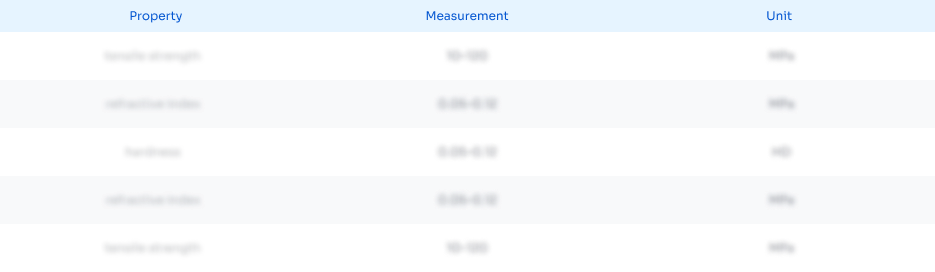
Abstract
Description
Claims
Application Information

- R&D
- Intellectual Property
- Life Sciences
- Materials
- Tech Scout
- Unparalleled Data Quality
- Higher Quality Content
- 60% Fewer Hallucinations
Browse by: Latest US Patents, China's latest patents, Technical Efficacy Thesaurus, Application Domain, Technology Topic, Popular Technical Reports.
© 2025 PatSnap. All rights reserved.Legal|Privacy policy|Modern Slavery Act Transparency Statement|Sitemap|About US| Contact US: help@patsnap.com