Thermal treatment process for improving weld structure performance of aluminum alloy battery box body
A technology of microstructure and properties of aluminum alloy, applied in the field of heat treatment process of aluminum alloy extrusion components, can solve the problems of welding microstructure and performance instability of heat-affected zone, so as to improve the microstructure and properties of aluminum alloy, reduce manufacturing cost and improve product quality and productivity effects
- Summary
- Abstract
- Description
- Claims
- Application Information
AI Technical Summary
Problems solved by technology
Method used
Image
Examples
Embodiment 1
[0021] Taking 6005 aluminum alloy extrusion profile as an example, its chemical composition is Al-0.50Mg-0.78Si-0.14Fe (mass percentage). Extrude the above-mentioned 6005 aluminum alloy extruded round ingot after preheating in the heating furnace. The temperature of the extruded profile exit die is 530°C, and it is simultaneously subjected to online forced air cooling and quenching. The temperature of the extruded profile entering the quenching zone is not lower than 460°C. , The cooling rate is above 60°C / min, and the first-time solid solution quenching treatment on the extrusion line is completed. The aluminum alloy extruded member cut to the specified length on-line is subjected to short-term aging at high temperature: 200°C / 1.5 hours.
[0022] The welding process of aluminum alloy extruded components adopts the automatic MIG welding method of welding robots. The welding conditions are: welding voltage 21V, welding current 180A, welding speed 800mm / min, welding thickness 5m...
PUM
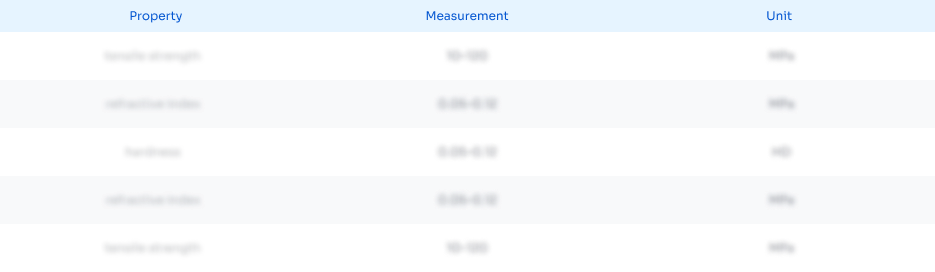
Abstract
Description
Claims
Application Information

- Generate Ideas
- Intellectual Property
- Life Sciences
- Materials
- Tech Scout
- Unparalleled Data Quality
- Higher Quality Content
- 60% Fewer Hallucinations
Browse by: Latest US Patents, China's latest patents, Technical Efficacy Thesaurus, Application Domain, Technology Topic, Popular Technical Reports.
© 2025 PatSnap. All rights reserved.Legal|Privacy policy|Modern Slavery Act Transparency Statement|Sitemap|About US| Contact US: help@patsnap.com