Method and device for sealing body of power station boiler
A power station boiler and sealing device technology, which is applied in the sealing of engines, components of steam boilers, steam boilers, etc., can solve the problems of increased installation workload, cross-operation coordination, civilized production and environmental protection, and difficulties in maintenance of refractory plastics and other issues, to achieve the effect of preventing fly ash from leaking out, being conducive to environmental governance, and eliminating ash accumulation on the top of the furnace.
- Summary
- Abstract
- Description
- Claims
- Application Information
AI Technical Summary
Problems solved by technology
Method used
Image
Examples
Embodiment 1
[0035] Embodiment 1: A method for sealing the roof of a power plant boiler, in the case of better working conditions, comprises the following steps:
[0036] 101. Treatment of the working face: Grinding and cleaning the working face where the boiler body crosses the wall tubes vertically and horizontally to form an expansion difference point, so that the working face is free of floating dust and rust.
[0037] 102. Determine the dead point of the seal: Weld stainless steel nails staggeredly on the horizontal working surface, the horizontal distance of stainless steel nail welding is 150mm, and the longitudinal distance is 100mm; bind stainless steel wire on the vertical wall pipe; the position of stainless steel nail welding and stainless steel wire The binding position is the transverse sealing dead point and the longitudinal sealing dead point, the area surrounded by the transverse sealing dead point is the transverse sealing dead point area, and the area surrounded by the lo...
Embodiment 2
[0040] Embodiment 2: Same as Embodiment 1, under the condition of harsh working conditions, it also includes before the embodiment step 104. It also includes the step of laying nickel-cadmium-manganese soft net: laying multi-layer nickel-cadmium-manganese inside the ceramic fiber layer The soft mesh, the ceramic fiber layer and the nickel-cadmium-manganese soft mesh are overlapped with high-temperature adhesives.
Embodiment 3
[0041] Embodiment 3: the same as Embodiment 1, except that it also includes the steps of: installing additional fixed steel wires: bundling steel wires on the stainless steel diamond-shaped steel nets between the wall-piercing pipes every 100 mm apart.
PUM
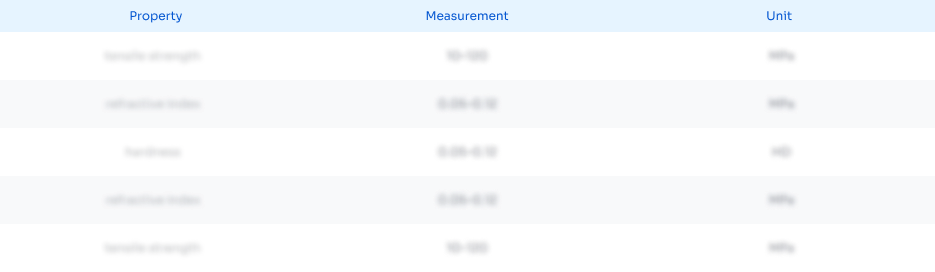
Abstract
Description
Claims
Application Information

- R&D
- Intellectual Property
- Life Sciences
- Materials
- Tech Scout
- Unparalleled Data Quality
- Higher Quality Content
- 60% Fewer Hallucinations
Browse by: Latest US Patents, China's latest patents, Technical Efficacy Thesaurus, Application Domain, Technology Topic, Popular Technical Reports.
© 2025 PatSnap. All rights reserved.Legal|Privacy policy|Modern Slavery Act Transparency Statement|Sitemap|About US| Contact US: help@patsnap.com