Integral electroplating waste water treatment equipment and process
A technology for electroplating wastewater and treatment equipment, which is applied in the fields of metallurgical wastewater treatment, water/sewage multi-stage treatment, neutralization water/sewage treatment, etc. , to achieve the effect of low operating cost, strong adaptability and convenient operation
- Summary
- Abstract
- Description
- Claims
- Application Information
AI Technical Summary
Problems solved by technology
Method used
Image
Examples
Embodiment 1
[0029] 1) Use hydrochloric acid to adjust the pH in the decontamination tank to 3.0, and add bleaching powder under stirring conditions, and react for 30 minutes. The added bleaching powder is calculated as 0.7kg / ton of electroplating wastewater;
[0030] 2) The waste water after the bleaching powder breaks the network flows into the ferrous sulfide packed bed for reaction;
[0031] 3) The effluent from the ferrous sulfide packed bed enters the coagulation tank, and alkali is added to the coagulation tank to adjust the pH to 8.0, and 200 g / ton of electroplating wastewater PAC coagulant is added, and the reaction is stirred for 7 minutes;
[0032] 4) Add 200ml / ton of electroplating wastewater into the flocculation tank, with a mass fraction of 0.5% PAM flocculant. Stir slowly for 2 minutes and enter the sedimentation tank. After flocculation and sedimentation, the produced water enters the clear water tank. The experimental results are shown in Table 1.
[0033] Table 1: Exper...
Embodiment 2
[0037] 1) Use hydrochloric acid to adjust the pH in the network-breaking tank to 2.5, and add bleaching powder under stirring conditions, and react for 20 minutes. The added bleaching powder is calculated as 1.0 kg / ton of electroplating wastewater;
[0038] 2) The waste water after the bleaching powder breaks the network flows into the ferrous sulfide packed bed for reaction;
[0039] 3) The effluent from the ferrous sulfide packed bed enters the coagulation tank, and alkali is added to the coagulation tank to adjust the pH to 8.5, and 50 g / ton of electroplating wastewater PAC coagulant is added, and the reaction is stirred for 10 minutes;
[0040] 4) Add 500ml / ton of electroplating wastewater into the flocculation tank, with a mass fraction of 0.75% PAM flocculant. Stir slowly for 1 min; enter the sedimentation tank, after flocculation and sedimentation, the produced water enters the clear water tank, and the experimental results are shown in Table 2.
[0041] Table 2: Exper...
Embodiment 3
[0045] 1) Use hydrochloric acid to adjust the pH in the pool to 3.5, and add bleaching powder under stirring conditions, and react for 30 minutes. The added bleaching powder is calculated as 0.7kg / ton of electroplating wastewater.
[0046] 2) The waste water after the bleaching powder breaks the network flows into the ferrous sulfide packed bed to react.
[0047] 3) The effluent from the ferrous sulfide packed bed enters the coagulation tank, and alkali is added to the coagulation tank to adjust the pH to 7.5, and 500 g / ton of electroplating wastewater PAC coagulant is added, and the reaction is stirred for 5 minutes;
[0048] 4) Add 100ml / ton of electroplating wastewater into the flocculation tank, with a mass fraction of 1.0% PAM flocculant. Stir slowly for 2 minutes and enter the sedimentation tank. After flocculation and sedimentation, the produced water enters the clear water tank. The experimental results are shown in Table 3.
[0049] Table 3: Experimental Results
[...
PUM
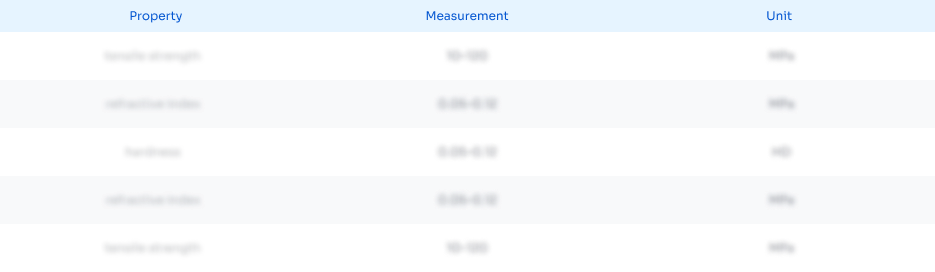
Abstract
Description
Claims
Application Information

- Generate Ideas
- Intellectual Property
- Life Sciences
- Materials
- Tech Scout
- Unparalleled Data Quality
- Higher Quality Content
- 60% Fewer Hallucinations
Browse by: Latest US Patents, China's latest patents, Technical Efficacy Thesaurus, Application Domain, Technology Topic, Popular Technical Reports.
© 2025 PatSnap. All rights reserved.Legal|Privacy policy|Modern Slavery Act Transparency Statement|Sitemap|About US| Contact US: help@patsnap.com